According to the latest International Energy Agency report, global production of crude steel continues to be dominated by conventional process routes. Reducing reliance on coal, which currently meets around 75 per cent of the energy demand of the sector, and increasing renewable electricity use are required to get on track with the net zero scenario. However, decarbonisation entails much more than just the electrification of the iron and steelmaking processes.
Green steel, according to Dr. Fleischanderl, is a comprehensive word that incorporates the transition to net zero, circularity, minimizing water consumption, energy efficiency, and lowering sound emissions in the steel industry. And, as a leading technology supplier, Primetals Technologies’ aim is to assist its clients in selecting and implementing the most efficient green steel solutions.
Being technology agnostic
Dr. Fleischanderl supports the notion that there is no ‘one size fits all’ solution for producing green steel. When striving to decarbonise, businesses must not back one single technology but rather push for a combination of best-possible solutions. “We have to get rid of fossil fuels; that is the logical first step, but reaching net zero will require deploying various technologies,” Dr. Fleischanderl continued to explain. “Electrification must replace the coal-powered route.” “Electric arc furnaces and related technologies become carbon neutral when steel producers use renewable energy sources, but electrifying as many processes as possible is critical,” he went on to say.
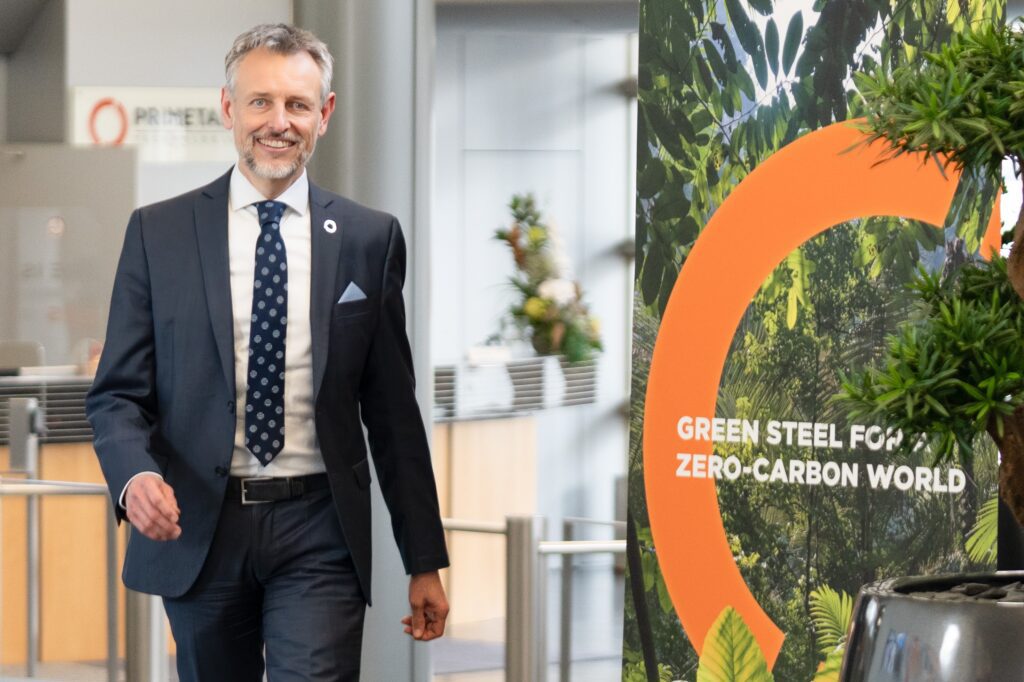
Dr. Fleischanderl emphasized the need for natural gas-based direct reduction as long as there is a scarcity of low-carbon hydrogen. “We insist on our customers considering hydrogen-ready technologies that will allow them to switch at any stage when it becomes available on an industrial scale.”
Furthermore, he stated that Carbon Capture, Utilization, and Storage (CCUS) might be a game changer, particularly in Asia. Dr. Fleischanderl elaborated on CCUS by highlighting LanzaTech’s technology, which uses off-gas from steel plants’ blast furnaces or Basic Oxygen Furnaces (BOF) to produce ethanol, which can then be converted in sustainable aviation fuel, packaging, and textile production, as well as perfumes and household cleaning products. Thus, the carbon is locked in a product, which usually is made from fossils.
Primetals Technologies is a close partner and shareholder in LanzaTech’s unique fermentation solution.
“By 2030, approximately 70 per cent of the world’s blast furnace fleet will require significant refurbishment. Steelmakers in the West are considering converting to DRI plants and EAFs, but in Asia, particularly India, there are many new blast furnaces that will rely on coal for a long time. As a result, for newer assets, CCUS may be the best solution,” he stated.
Another crucial piece of the decarbonisation puzzle according to Dr. Fleischanderl is the usage of “crafted scrap”. As per Primetals Technologies’ scrap models, there will be 500 million tons more scrap in 2050 than now, although overall steel capacity will only increase by half.
“While we do not anticipate a scarcity of scrap until 2050, it all boils down to quality.” “Scrap is purchased in accordance with the specifications, but you never know what you’ll get in the end,” he explained.
To produce high-quality steel grades, steel producers usually need chemically pure and pre-sorted scrap. Unwanted goods should be identified and removed. To ensure that the composition of scrap matches the product, different scrap qualities must automatically be identified in the yard and supplied to the production process. The process of identifying, cleaning and supplying specially selected “crafted scrap” allows a greater amount of scrap to be used in higher-quality grades.
Primetals Technologies boasts of innovative scrap treatment and cleaning techniques based on digitalisation and artificial intelligence.
Beacons for a sustainable future
Dr. Fleischanderl highlighted some key innovations and projects that Primetals Technologies is currently involved in.
A “lighthouse project”
The HYFOR and Smelter industrial prototype plant in Linz, Austria isa collaboration between Fortescue, a global leader in the mining and heavy industries, globally leading steel and technology group voestalpine, Mitsubishi Corporation, and Primetals Technologies. .
Hydrogen-based fine-ore reduction, HYFOR, is the world’s first direct reduction method for iron ore fines, eliminating the need for agglomeration processes such as sintering or pelletizing. Since the end of 2021, a pilot plant has been in operation, and the technology is now ready for scale-up.
On December 19, 2022, all the strategic partners signed a Memorandum of Understanding (MoU) aimed at designing and engineering an industrial-scale prototype plant with a new process for net-zero-emission ironmaking at the voestalpine site in Linz, Austria.

“We intend to build a continuously operating about 3 ton per hour scale industrial prototype plant with a Smelter unit.” “We want to be able to run on both low-grade and high-grade iron ores.” “Voestalpine’s green hydrogen will be used to reduce the iron ore.” The resulting DRI and alternative green hot metal will have the industry’s lowest carbon footprint.” “Because this is a massive project that requires a significant investment, we have recently applied for funding at the European level.” The final investment decision for the project will be made in early November,” Dr. Fleischanderl explained.
The launch of GravitHy
In June last year, GravitHy, was launched by an industrial consortium composed of Primetals Technologies, EIT InnoEnergy, Engie New Ventures, FORVIA, GROUPE IDEC, and Plug.
The fully sustainable iron company will support the growing demand for low-carbon DRI, whilst contributing to Europe’s “Fit for 55” package ambitions to decarbonize hard-to-abate industries. The project, which plans to mobilize 2.2 billion euros worth of investment at commissioning, will build its first plant in Fos sur Mer, Southern France, with construction commencing in 2024. The company aims for the plant to be fully operational by 2027, subject to any required regulatory approvals. GravitHy has the ambition to produce an annual throughput of 2 million tons of DRI and to create over 3,000 direct and indirect jobs for the region.
Arvedi ESP – the disruptor
Dr. Fleischanderl picked this one because of its high-potential status. “Unfortunately, even in these modern times, the steelmaking process remains unintelligent. It is an age-old process that requires cooling down and reheating several times to go from sinter feed to near-end products,” he said.
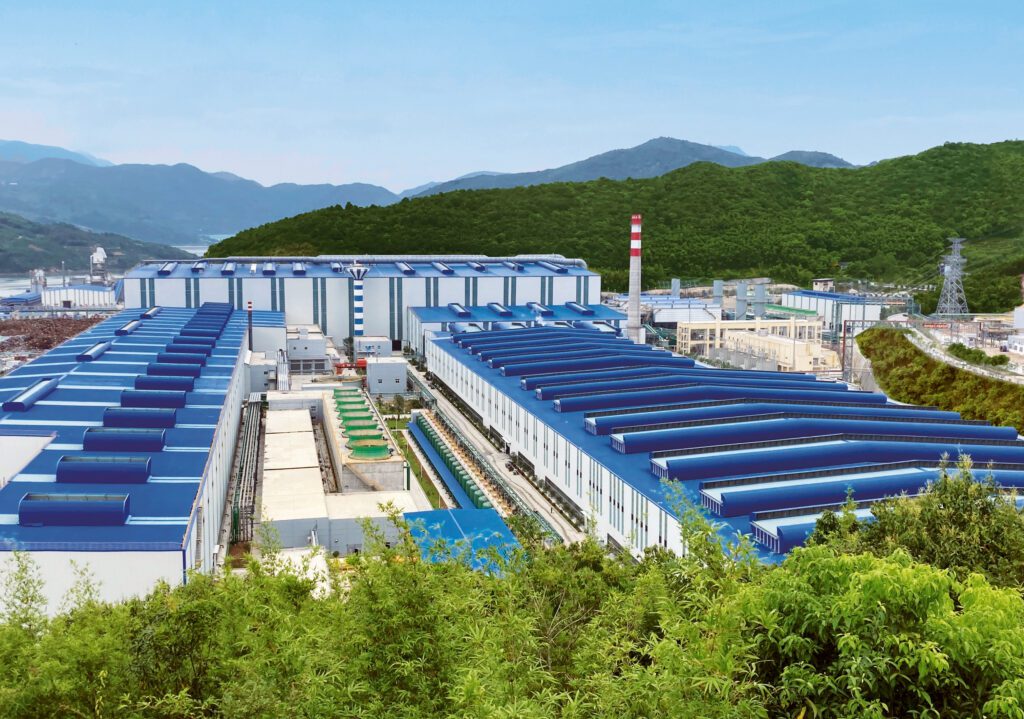
The Arvedi ESP process, the only one in the world being 100% electrified, produces hot strip in a combined, continuous, and uninterrupted casting and rolling process. In this type of plant, the energy consumption and the associated costs are up to 45 per cent lower than those of conventional casting and rolling processes. This also means a significant reduction in CO2 emissions, compared to conventional casting and rolling route up to minus 95%. The Arvedi ESP process operates successfully since 2009 at the steelworks of Acciaieria Arvedi S.p.A. (Arvedi), Italy, as well as at numerous other locations across the world. Several Arvedi ESP plants will be implemented over the next few years.
Salzgitter Low CO2 Steelmaking (SALCOS) – the first real road check
In August 2023, German steel producer Salzgitter AG ordered a state-of-the-art EAF Ultimate from Primetals Technologies to replace a coking-coal-based steelmaking process with a fully electrified unit. With a tapping weight of 220 tons, the furnace will have an annual capacity of 1.9 million tons of steel. The production of green steel is scheduled for the end of 2025.
“There have been many pledges and announcements from European steel producers over the last year, but SALCOS was the first one to be executed. We are proud to also supply a comprehensive environmental package including the world’s largest Waste Heat Recovery at an EAF, to minimize all the emissions from this new operation as far as possible,” expressed Dr. Fleischanderl.
Hydrogen – key solution and key roadblock
Green hydrogen has emerged as one of the most promising prospects for helping decarbonise hard-to-abate sectors, taking us a step closer to carbon neutrality but there’s a catch.
Green hydrogen is not yet commercially available at scale, and hence still more expensive than conventional options.
“Steel is clearly stated as a high priority on the clean hydrogen ladder because there is a shortage of solutions to decarbonise the sector.” “Electrification, hydrogen, or the use of natural gas as an intermediate step are the only ways to remove the oxygen from the iron ore,” he emphasized.
Dr. Fleischanderl believes that the early movers would gain immensely, but that government help will be critical in order to scale up hydrogen production capabilities.
Praising the Biden administration’s Inflation Reduction Act, Dr. Fleischanderl said that this move will bring hydrogen to a competitive level in the United States, but he thinks there is still a huge gap as far as Europe is concerned.
He is also optimistic about the CBAM’s role in addressing the risk of carbon leakage and reinforcing the EU ETS.
For him, however, the most straightforward approach remains the market’s willingness to pay a premium.
“With these three pillars in place, green steel can become competitive against grey steel, provided there is a global regulatory framework that is transparent and easy to understand,” Dr. Fleischanderl expressed.
Ahead of the curve
While Dr. Fleischanderl repeatedly stated throughout this conversation that Primetals Technologies holds the position of a market leader in environmental innovations for the metals industry, the company is clearly ready to switch gears. He enumerated several factors that reinforce the company’s position as the global front-runner.
- Mitsubishi Heavy Industries (MHI), the parent company of Primetals Technologies, aims to be carbon neutral by 2040.
- Primetals Technologies has established a report on Scope 3 emissions of delivered plants as part of MHI’s net-zero mission.
- MHI is quite active in the hydrogen ecosystem – generation, compression, storage and shipping of hydrogen.
- The synergies with MHI put Primetals Technologies in a unique position.
- MHI is a leading company in carbon capture with its unique KM-CDR process. Primetals Technologies is now adapting this technology for the steel sector and actually installing a pilot unit at ArcelorMittal in Ghent
- Hydrogen-fired gas turbines as a backup for energy systems.
- Partnerships and collaborations.
The time is now
Dr. Fleischanderl briefly touched upon the importance of sustainable finance in the decarbonisation of the steel industry. “It is being estimated that an investment of 1.3 trillion USD is needed to transition the whole sector and the public sector needs to do most of the heavy lifting.” “There is no other way out.” “If you don’t set your plan right now, it’s already late. Soon, the market is going to demand green steel.”
Before concluding the conversation, Dr. Fleischanderl encouraged the new generation of talent to work in the steel industry to make a positive impact on people and the planet.