By using advanced manufacturing technologies to meet commercial requirements, an innovative Australian company named BioCarbon offers valuable renewable carbon products produced from low-value biomass streams. One of their products has been successfully trialled in two electric arc furnaces in Australia. Green Steel World sat down with Mr. John Mellowes, director of BioCarbon, to discuss their technology and products in detail, and to find out why biocoke should be one of the steel industry’s go-to solutions.
It all started five years ago when John Mellowes, Chad Sheppeard, Kannappar Mukunthan and Mark Willcocks decided to join forces and capitalize on their long-time expertise. Coming from a wide range of sectors, such as civil engineering, mechanical engineering, metallurgy and arboriculture, they established a company with the sole purpose of transforming woody agricultural waste into renewable carbon and energy products intended for industrial applications. Their Biocarbon bricks can fully replace fossil coke in the steelmaking process in an electric arc furnace.
Mission sustainability: accomplished
The secret recipe for BioCarbon’s flourishing business is pyrolysis: the heating of an organic material, such as biomass, in the absence of oxygen. Depending on the feedstock used, this process has the potential of being one hundred percent sustainable, which is exactly what attracted Mr. Mellowes and his colleagues in the first place. By using woody biomass, they are ensuring that the process remains green, with zero waste. In addition, they are stopping a lot of that waste biomass from going to landfill.
“The woody biomass, such as woodchips, sawmill waste, green waste and agricultural waste, is heated at around 550 °C in the pyrolysis machine. The three products that are obtained are charcoal which is used to make biocoke, syngas that can be burned for heat or used for generating electricity, and a watery product called wood vinegar which is used in agriculture,” Mr. Mellowes briefly described the process taking place at BioCarbon’s facility in Sydney.
As Mr. Mellowes kindly continued to explain, the charcoal obtained is a 95% fixed carbon product, however, in this phase, it is still not dense nor mechanically strong enough to be used in a furnace. He quickly elaborates on this, “If we used the charcoal in a furnace, it would simply float on top of the melt, react with oxygen and be emitted as CO2. It is very brittle. By the time it reached the furnace, it would simply be turned into dust due to mechanical wear. Therefore, we take the charcoal and process it to make it a great deal denser and stronger, and all of that in the form of so-called Biocarbon bricks. These bricks can handle the “rough ride” into the furnace. Once they are inside the furnace, due to their appropriate density, they will float at the right level and successfully do the job of removing the oxygen from the iron.”
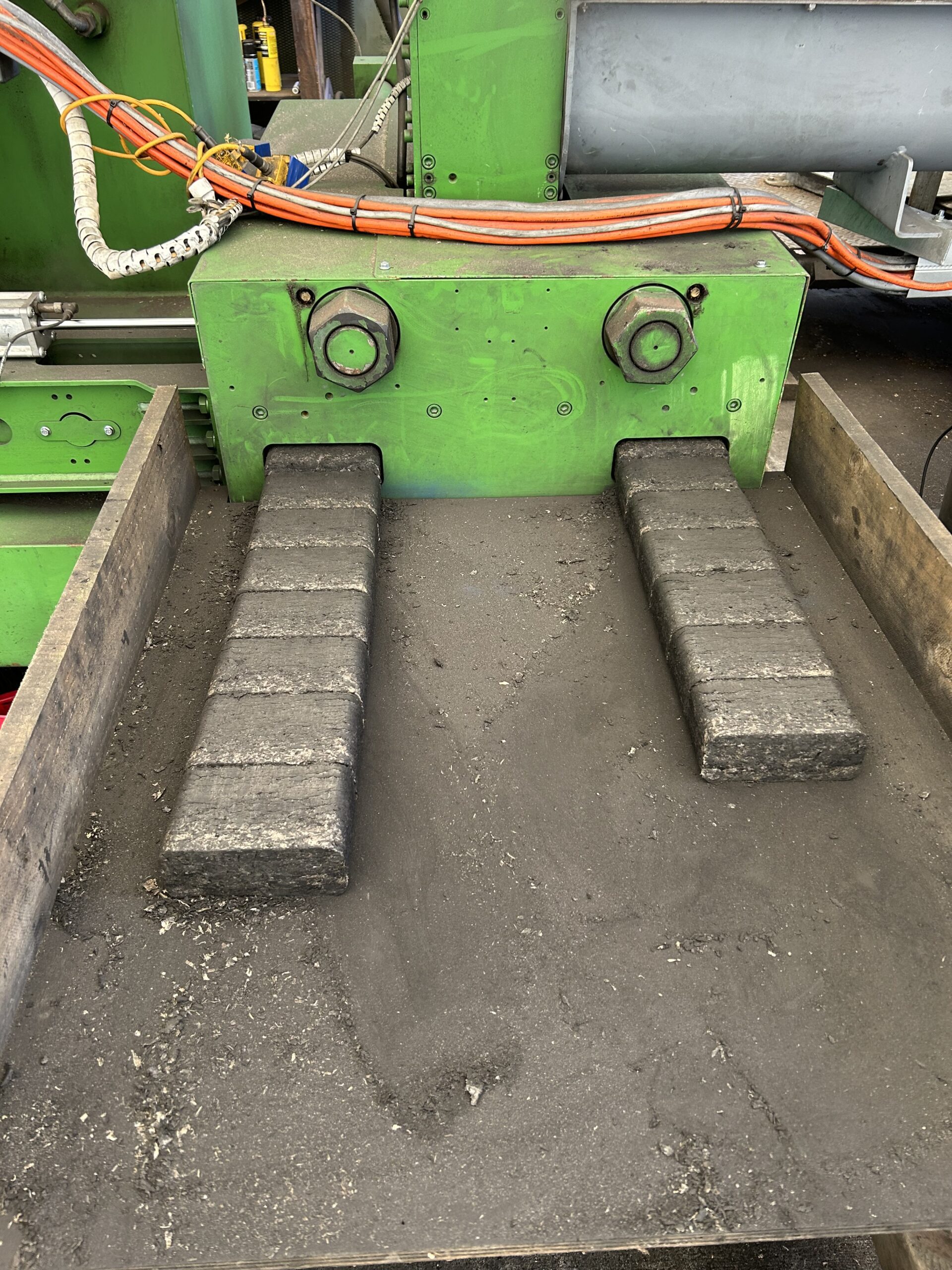
The pyrolysis machine or biomass converter as some call it, was designed by Mr. Mellowes and his colleagues. “We wanted to design a machine that would ensure the capital expenditure matched the price of the product. We have decided to act upon our own ideas and it paid off. We are truly satisfied with our machine and what makes us even more excited is the fact that we believe that scaling it up is highly probable.”
Members of the BioCarbon’s team had been perfectly aware that overcoming obstacles represents one of the usual stages on the path to success. Proud of the company’s journey, Mr. Mellowes stated, “We have gone through a lot of heartache and plenty of setbacks in the beginning, however, developing new technology is not an easy task, and hitting walls is inevitable. But all the hardships proved to be worth going through because now we can confidently say that we have a reliable and robust technology platform that we can move ahead with.”
Acknowledging the advantages
Mr. Mellowes briefly touched upon the particularities of the use of BioCarbon’s biocoke in an electric arc furnace (EAF). “In an EAF coke is mostly used in terms of charge carbon, inject carbon and recarburizer. Charge carbon is used in the initial stage when iron is being heated while inject carbon is used a bit later in the process. After steel finds its way into the ladle, it is tested to see if carbon levels are high enough. If the levels are too low, a recarburizer will be used to adjust carbon levels. Our product is mostly used as charge carbon; however, we have developed products for injection and recarburization as well. With the use of green electricity, we have truly green steel.
CO2 is still emitted using biocoke however it is the source that counts. Because it comes from waste streams that would eventually break down into CO2 either way, biocoke is carbon neutral. The alternative to this is the traditional coke which adds CO2 to the atmosphere from fossil sources.

Preliminary testing of the product was done by the University of New South Wales. “We wanted to make sure that everything is perfectly in order and that there is no risk of damaging the plant,” Mr. Mellowes explained.
He continued, “Over the last year and a half, we have replaced coke in two EAFs. In the beginning, we blended our product with fossil coke 50/50 but soon moved straight onto 100% replacement. Neither EAF operator noticed any abnormalities in their normal operating conditions. There was no change in steel or slag chemistry, gas or power consumption, etc. Several thousands of tonnes of steel have been made so far with our product and a lot more will be produced in the future, seeing as we have just delivered ten tonnes of product to one of the EAF operators.”
BioCarbon’s mission received wide recognition. They have been awarded a grant from the Department of Industry, Science, Energy and Resources of around three hundred thousand Australian dollars. Mr. Mellowes emphasized that he believes this is money very well spent.
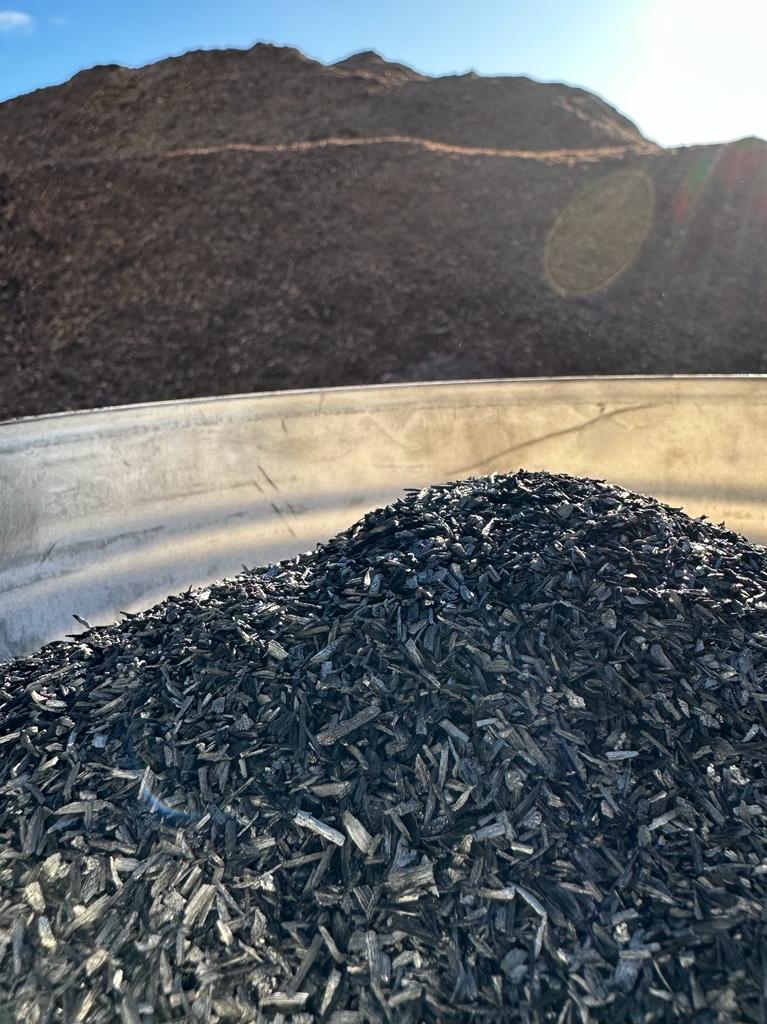
It is all about the scales matching
While the dispersity of raw material does complicate matters, BioCarbon is successfully navigating the market and overcoming possible issues related to the availability of biomass. “There is plenty of biomass in Australia, however, it is not concentrated in one place. You will find twenty thousand tonnes of material per year in one place and twenty thousand an hour down the road perhaps. If you build a large plant somewhere in Australia, you would struggle to feed it because locally, material would be scarce and the transport costs would make it uneconomical. Whereas the scale we are doing to produce Biocarbon bricks is quite a nice fit because, from one timber mill, we can produce enough for an EAF plant in Sydney, for example,” Mr. Mellowes explained.
No additional costs
What makes most of the green technology so undesirable is the price. BioCarbon boasts a product that enables steelmakers to decrease their carbon footprint without incurring large capital costs seeing as no modification to the existing equipment is needed. “Our product is a direct replacement for traditional coke. No modifications of the process nor the equipment need to be done to be able to implement our product. Moreover, we expect the price to be very stable and, long-term, the same as the price of fossil coke.
A bright future awaits
Mr. Mellowes revealed that they intend to build more and more plants as they go along, encouraged by charcoal’s potential to be used in a wide range of sectors, not only steel. “We are still in our early days. Nevertheless, we have received interest from steelmakers all over the world. They recognize the importance of our product so I would dare to say that the market is looking very good for us. With steel being an irreplaceable material, the demand for it will only increase. Direct reduced iron is considered to become the main replacement for blast furnace operations. If DRI is made, it will likely be accompanied by an EAF. And that EAF will need some form of carbon.”
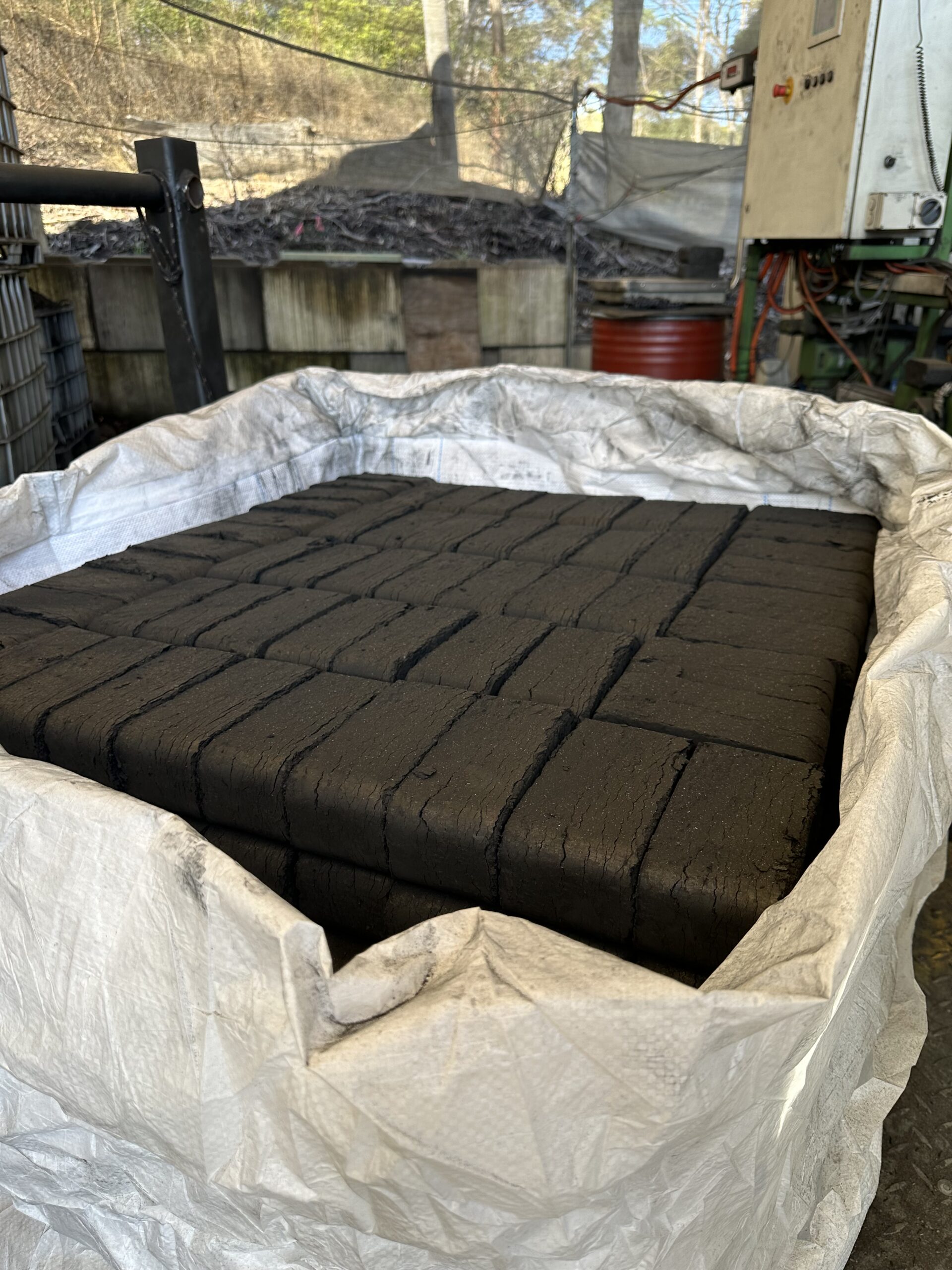
without incurring large capital costs.
What BioCarbon is now in search of are good partners in the steelmaking world that could help bring the global reach that Mr. Mellowes and his team are looking for.
He is very confident about their product and has full trust in the ability to help EAFs produce sustainable steel. “We have seen the product work successfully and we remain on that path. There is no other option than being confident about its ongoing success. As the race for the salvation of our world is uncertain, we must do everything in our power to win it. I think this is one small step, one, let us say, “brick” in the wall towards a decarbonised world,” he concluded.