Green steel has been a topic of discussion for some time, but defining it remains complex and often overwhelming. However, one fundamental truth stands out: steel is indispensable to our way of life, transportation, and work. Mr. Heinhuis highlighted this point as he began our insightful conversation:
“Steel as a material is inherently sustainable, but its production is not yet sustainable. That is the next critical step. Historically, customers valued steel for its mechanical properties, strength, and quality. Now, to distinguish sustainably made steel, we need a clear definition. Green steel does not differ from conventional steel in terms of mechanics, chemistry, or strength, but it stands apart in societal and sustainability terms. We need to articulate that.”
Moreover, decarbonizing the steel sector supports the decarbonization of numerous other industries, including construction, automotive, energy, manufacturing, and transportation. By greening the steel industry, we contribute significantly to reducing carbon emissions across these interconnected sectors.
Steel is well-positioned to achieve these sustainability goals. Mr. Heinhuis emphasized that CO2 emissions are not inherent to iron and steelmaking. “We currently rely on coal, which causes CO2 emissions, but there are methods to produce iron from ore without CO2 emissions,” he explained. “This differs from, for instance, cement production, where CO2 is an inevitable byproduct. In steelmaking, we can significantly reduce CO2 emissions. While reaching zero emissions might be challenging, we can drastically cut them.”
Expanding on this, he further outlined Tata Steel Nederland’s ambitious goals to be carbon neutral by 2045, with a major milestone in 2030. They plan to replace a blast furnace with a DRI-EAF (Direct Reduced Iron – Electric Arc Furnace) installation, initially using natural gas and transitioning to hydrogen. Given current market conditions, economically viable hydrogen may not be available by 2030, so they will start with natural gas, leading to a 40% reduction in site-level emissions, potentially higher at the product level.
The chosen technology has distinct elements. “We will continue using a combination of ore and scrap in our steelmaking, allowing us to produce clean, high-performing steel. Our robust secondary steelmaking processes, combined with ore-based and scrap-based methods, allow us to produce advanced green steel sustainably,” Mr. Heinhuis elucidated.
Furthermore, Tata Steel’s sustainability agenda extends beyond liquid steelmaking. Mr. Heinhuis detailed strategies for reducing emissions in processes like rolling and coating. “While the biggest impact is in liquid steelmaking, we also have strategies for decarbonizing rolling, annealing, and coating,” he explained.

The Zeremis solutions
“Collaboration with customers, partners, and markets is crucial. That is why we conceived Zeremis as a journey—a journey towards zero carbon emissions and a circular world,” stated Mr. Heinhuis as we delved into the topic of Zeremis.
Zeremis® is central to Tata Steel’s commitment to becoming carbon neutral by 2045. Achieving this ambitious goal involves a multi-step process, recognizing that each stage of the transition requires unique solutions. While Tata Steel Nederland is on a promising path to meet its 2030 and 2045 targets, the company understands the need for immediate action. Zeremis will introduce tailored solutions at every phase of this transition. Currently, only a small amount of embodied green steel is available in the market, as the shift towards DRI and other sustainable steelmaking methods will take time.
Mr. Heinhuis elaborated on the holistic approach of Zeremis: “Zeremis goes beyond being a mere commercial offering; it is a collaborative approach in the value chain, inviting customers and partners to join the journey towards a carbon-neutral, circular world. This journey encompasses multiple pillars to decarbonize the entire steelmaking process—from producing liquid iron from ores, to casting, rolling, coating, and the final steel processing within Tata Steel Nederland. Additionally, Zeremis addresses the carbon-neutral transport of steel products to customers and is committed to enhancing circularity by increasing recycled content ensuring the value of scrap is retained within the value chain.”
Zeremis offers a suite of solutions that develop over time to meet the demands of the value chain at every step of the transition. Currently, three commercial solutions are available under Zeremis: Zeremis Carbon Lite, Zeremis Delivered, and Zeremis Recycled. These solutions enable customers to take responsibility and act now, though they will differ from the solutions available by 2030 years when significant changes, such as taking the first blast furnace out of production, are implemented.
Zeremis Carbon Lite helps customers reduce their scope 3 emissions now, using a mass balance approach where direct carbon avoidance projects in Tata Steel´s production route are allocated to specific customer orders. This allows customers to meet their immediate emission reduction targets. “Zeremis Carbon Lite is a flexible solution that allows our customers to choose the CO2e intensity reduction that they need. These CO2e savings can be reported as a reduction in a company´s scope 3 emissions,” Mr. Heinhuis stressed. The fact that this solution is verified by DNV, an independent assurance expert, further confirms its value. Waelzholz Group and Stahlo Stahl Service, amongst others, have already placed their trust in Tata Steel by signing MoUs for the supply of Carbon Lite. Once the IJmuiden steel plant launches its new steelmaking route, the plan is to transition the supply to Zeremis embodied carbon reduced steel.
While similar to Carbon Lite, Zeremis Delivered focuses on decarbonizing outbound transport by targeting transport emissions. This declaration-based solution uses HVO100 instead of conventional diesel to fuel trucks, offering a 90 percent reduction in CO2e intensity. “Both Carbon Lite and Delivered enable us to deploy carbon savings in our production and transport systems, creating a business case for additional direct carbon avoidance measures,” he explained.
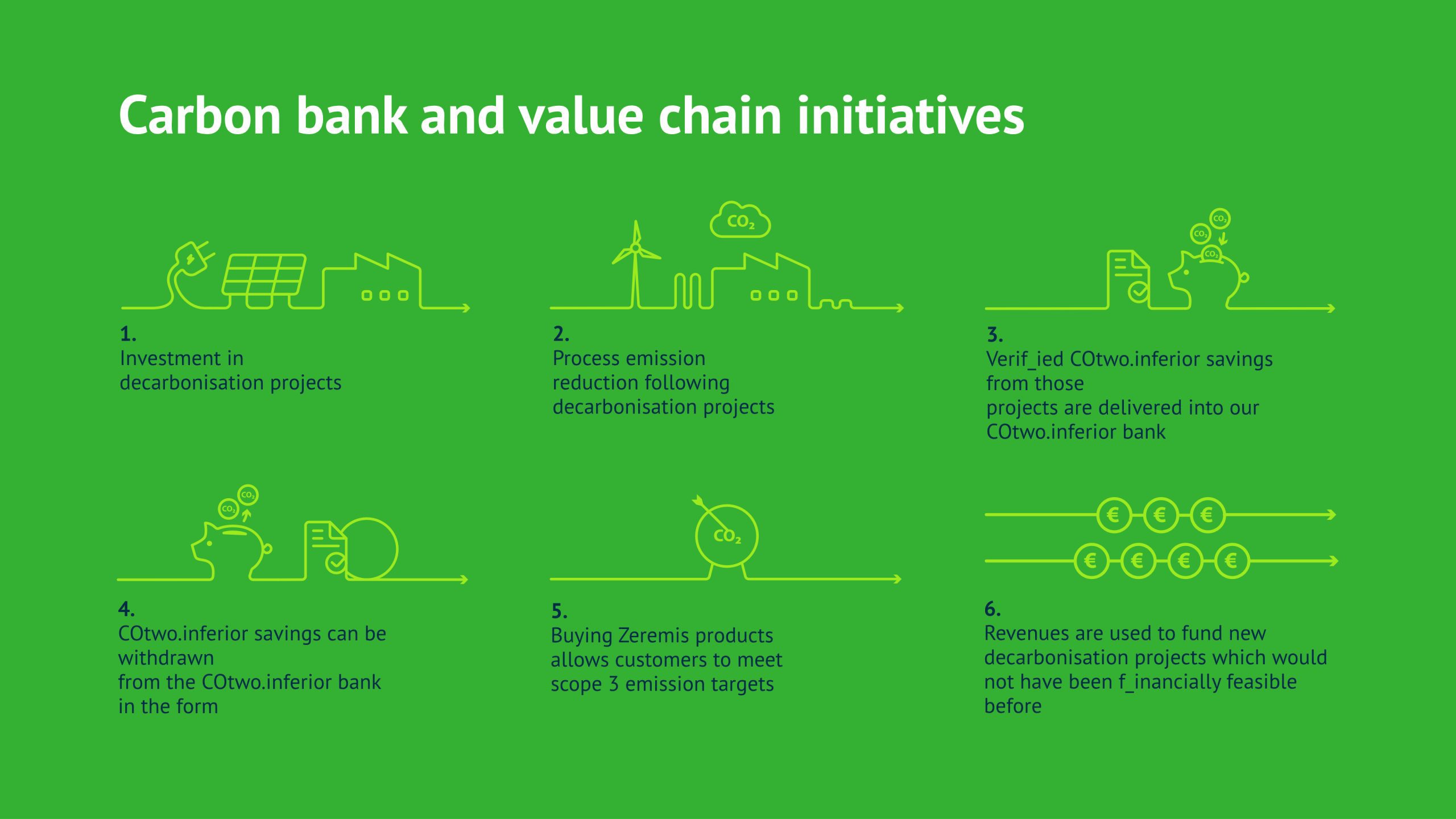
Zeremis Recycled, the newest addition to the Zeremis lineup, was launched in June 2024. Discussing this initiative, Mr. Heinhuis said, “Zeremis Recycled promotes circularity by increasing our scrap intake and allocating it to customer orders. This helps customers claim higher recycled content, especially for advanced steels. The goal is to retain the value of scrap by returning it as advanced steel, ensuring that high-value scrap is not just re-melted but utilized in producing new, high-performing products.”
He concluded, “Steel’s high recyclability is well-known, but our focus is on retaining the intrinsic value of scrap and reintroducing it as advanced steel. Zeremis Recycled embraces this principle, aligning with our role as an advanced strip steelmaker.”
Understanding the material
When asked about Tata Steel Nederland’s DataDrivenSteel initiative and its contribution to sustainability goals, Mr. Heinhuis pointed out the versatility of steel. “Steel is incredibly versatile due to the ability to fine-tune its properties through alloys, rolling, and heat cycles, meeting specific processing conditions and application requirements,” he said. “This versatility is a strength, but it also demands a deep understanding of how to achieve these tailored properties. That is where data and data models in steel production become crucial.”
He elaborated on the role of data in optimizing steel production processes. “We use data extensively to understand and control our process conditions, enabling us to produce advanced steels for demanding applications. As we transition to new steelmaking technologies, such as the Electric Arc Furnace and its associated secondary steelmaking processes, the importance of data grows even more.”
In summary, he underscored the relevance of data in their operations: “The more we understand the material through data, the stronger our modeling and steering capabilities become. This enhances our product development and allows us to produce advanced steel grades more efficiently and sustainably. Material tracking throughout the steel value chain will also make it more visible where the big changes in carbon footprint occur.”
As our discussion drew to a close, Mr. Heinhuis stressed the critical importance of collaboration: “Collaboration in the value chain is incredibly relevant because carbon footprints accumulate throughout the entire chain. For instance, as a materials producer, we have significant scope 1 and 2 emissions, while our customers mainly face scope 3 emissions. This is true across various industries, from construction and automotive to packaging and mechanical engineering. The brand owners and end users in these industries can only achieve their sustainability goals if they address their scope 3 emissions. Given that those at the end of the value chain are primarily impacted by scope 3 emissions, our role as a materials producer is vital. We have the responsibility and the capability to reduce emissions. This is why collaboration is so essential.”
The multi-phase, long-term nature of Tata Steel Nederland’s complex sustainable transition affirms Mr. Heinhuis’s assertion that they are deeply committed to not only greening their own operations but also advancing the broader sustainability agenda.
Innovating packaging
Tata Steel Nederland’s involvement in the packaging industry might be less known than their involvement in, for instance, automotive industry, but it is a significant part of their sustainability strategy. The company’s Protact® packaging steel, a tin-free polymer-coated alternative to traditional lacquered steel, reduces volatile organic compounds and eliminates the need to draw upon scarce tin resources thereby supporting a more sustainable can production process. This innovation not only enhances the durability and sustainability of packaging but also demonstrates Tata Steel Nederland’s commitment to improving the environmental footprint of everyday products.