Aware of the challenges and professional risks, Mr. Steinar Danielsen, co-founder and Chief Executive Officer of WAI, and Dr. Gang Xin, co-founder, and Chief Technology Officer of WAI, are confidently following the path towards the end goal: making the world we live in a better place. Green Steel World gladly accepted the opportunity to sit down with Mr. Danielsen and Dr. Xin for an interview and to hear more about WAI´s vision of the industry as well as the company´s plans for the future.
By Lucija Kozina
The European steel industry contributes 1.3% of the total European GDP (2021 data) but also 8% of the total CO2 emissions. Large subsidies have been spent on the EU level as well as on national levels to help the industry decarbonise. Aside from grants, large funds and equity investors are contributing to this unprecedented industrial infrastructure transformation. Hydrogen and carbon capture and storage and utilization are considered the mainstream technologies for the decarbonisation of the steel industry today.
If we went back in time several hundred years, we would find out that the steel industry started by using charcoal (biocarbon) as a reducing agent for stripping oxygen from iron ore and producing iron. Almost 150 years ago, the higher-in-quality and more easily obtained coal came into the picture and replaced charcoal.
Founded in 2017, WAI is, in a way, guiding the industry on a journey to where it all started. Simply put, they are replacing fossil carbon with biocarbon for the metallurgical industry. “We have developed the technology to produce high-quality biocarbon whose density and mechanical and thermal resistance satisfy the necessary requirements for direct replacement of fossil carbon,” said Dr. Xin, as we dived into the topic. “Our process is a combination of conventional methods such as pyrolysis and biocarbon formulation technologies. By implementing new technologies in a conventional bioenergy plant, we do not only produce bioenergy but also material such as biocarbon. Pyrolysis itself has recently seen many advancements. The technology is highly scalable and can enable a large production provided that the feedstock sources are stable,” he continued.
Sawdust, bark, wood chips and shavings and waste wood sorted from municipal solid waste represent the feedstock that has the potential to be transformed into biocarbon. Each tonne of biocarbon can replace up to 1.3 tonnes of fossil carbon which equals 3.3 tonnes of CO2 emission reduction, based on WAI´s product CO2 footprint analysis.
“At the moment, charcoal is mainly produced from hardwood in Brazil and Southeast Asia. The process is not only energy-inefficient but also entails long and costly transportation. In our opinion, the best solution would be to use the forest residue or waste wood locally in order to produce high-quality biocarbon which can replace metallurgical coal and coke directly in the steelmaking process without changing any properties of the final products and without any changes to the steelmaking facility needed. That way no large investments would be incurred for the steel companies,” Dr. Xin commented.
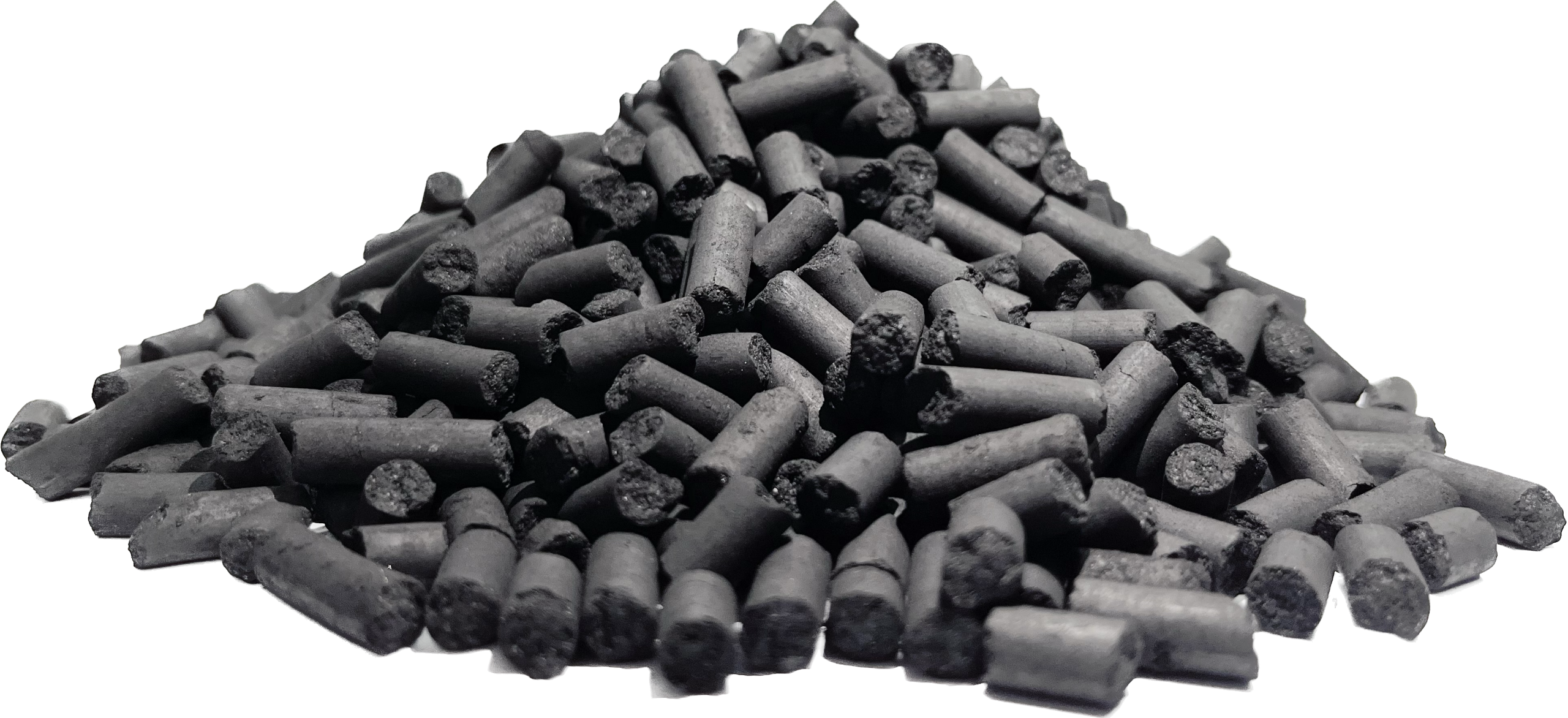
Biomass is better for material recycling according to the EU RED III
With the total available sawmill by-products and demolition wood (types A, B and C) in Europe, there is potential for 10-12 million tonnes of biocarbon. Compared to sixty million tonnes of metallurgical coal being imported to Europe, this represents a significant decarbonisation potential. “We need more feedstock brought into the picture such as forest logging residue, waste wood, pulp and paper and biorefinery waste. If this was achieved, we would be able to go up to twenty or thirty percent of the total demand. We believe that hydrogen will be the main decarbonisation tool by 2050, however, biocarbon can still contribute a 10-20% emission reduction to the overall European CO2 emissions from the steel industry during the transition period. Even if hydrogen technology is eventually implemented and most of the existing BFs are replaced by electric arc furnaces (EAFs), large amounts of biogenic carbon materials will be needed in EAFs, which will maintain the demand for biocarbon,” Dr. Xin explains.
When asked about the availability of feedstock, Mr. Danielsen kindly elaborated on that topic and on WAI´s satisfaction with the market in general. “If we go back two or three years, the feedstock availability has been very good. Sawmills often sell their products at low prices because they lack storage space. Due to the energy crisis and the consequential worry that appeared regarding bioenergy, the prices for the mentioned by-products skyrocketed. However, we are witnessing the crisis slowly coming to an end which will result in a drop in prices during the next one or two years. The Cascade principle in the new EU’s Renewable Energy Directive (RED III) states that woody biomass should be used according to its highest economic and environmental added value, which will guide the wood industry to implement more recycling solutions than bioenergy applications, such as biomass combustion. Biocarbon would be a good choice of material recycling for forest residue and waste wood. It would boost sustainability levels for sawmills and waste wood handling companies.”
A business model that benefits all
WAI´s business model not only benefits the steel industry but also the wood industry. Seeing as sawmills do not have a good solution for their by-products, they are obligated to transport them to other facilities, for example, paper mills and combustion plants. Due to the bulkiness of the product and the water content that can be higher than 50%, the value of the biomass is reduced during transportation.
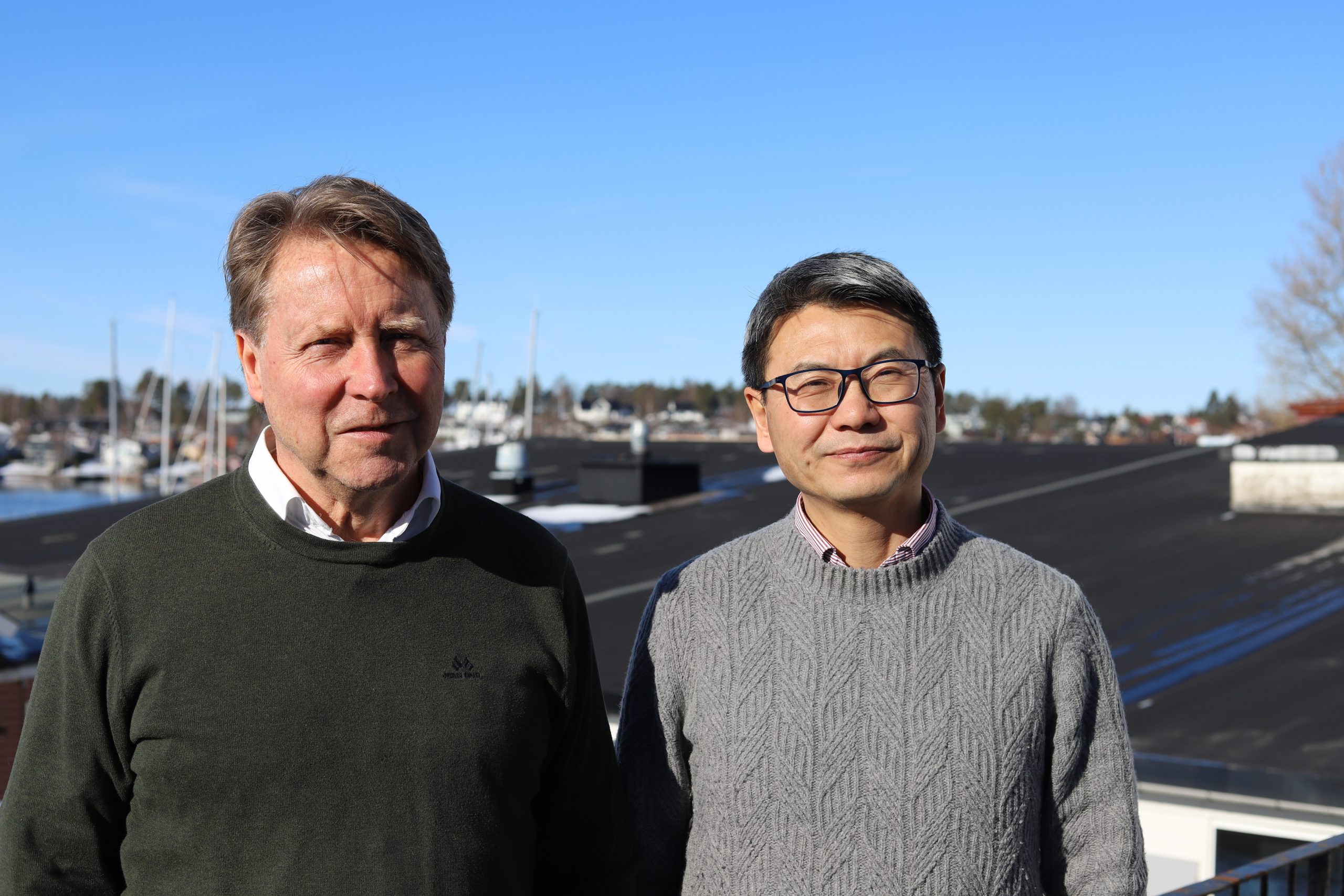
Highlighting once again the wide range of sustainable strategies at our disposal, Dr. Xin proposed a suitable solution. “By setting up our biocarbon production facility inside the sawmill, we would be able to take the by-products on-site, produce biocarbon and make pellets. This would in turn reduce up to 90% of the facility´s potential truck traffic.”
Syngas is the secondary product obtained in WAI´s sustainable manufacturing process. It provides the option to produce hot water, steam and electricity thanks to a technology called Organic Rankine Cycle. “If we implemented our technology in sawmills, we would be able to send thermal energy back which allows them to avoid having to invest in new boilers or new flue gas treatment facilities,” explains Dr. Xin.
WAI´s founders are certain that after the steel industry recognizes the full potential of their biocarbon technology, the wood industry will soon follow. “There is a fixed schedule for replacing existing boilers in Norway and other European countries. We hope to go through with our plan and show companies that a more sustainable and cost-effective option exists, rather than spending money on new boilers or transporting biomass to combustion facilities,” Mr. Danielsen stated.
Endless potential
Currently, WAI boasts a large-scale demonstration plant that can process three hundred kilograms per hour. In other words, they are able to produce up to five hundred tonnes of biocarbon per year. The next step will be the commissioning of a full-scale five thousand tonnes/year biocarbon plant in 2025.
“We have several products. Our injection biocarbon is designed for injecting into a furnace through pipes after pulverization. At the moment, the market is huge, however, due to the expected replacement of BFs with EAFs, the market will be shrinking. This is why we have developed our second product, charge biocarbon. Its thermal and mechanical resistance makes it suitable for use in EAFs,” Dr. Xin elucidates. “We are also developing our charge biocarbon to meet the requirements of silicon, ferrosilicon, ferromanganese, and aluminum industries. We are working closely with SINTEF, one of the largest European research institutes, on the demands of ferroalloy industries. Their expertise and experience boosted our product development greatly.”
WAI´s team is aware of the importance of proving feasibility. Once they establish a full-scale proof-of-concept plant, they will use this licensing model to work with feedstock suppliers and establish facilities globally. Around four million euros from the Norwegian government has been secured for this goal with another eight million in grants from European and Norwegian funding agencies for the advancement of their biobased carbon product development. “When the proof-of-concept plant is ready and the risk further reduced, this business model will be rolled out quickly due to the huge demand. We actively seek close cooperation with the metallurgical industry and equity funds. The biocarbon industry is young but it is growing fast, and we need more capital to accelerate the industry transformation,” Mr. Danielsen stated.
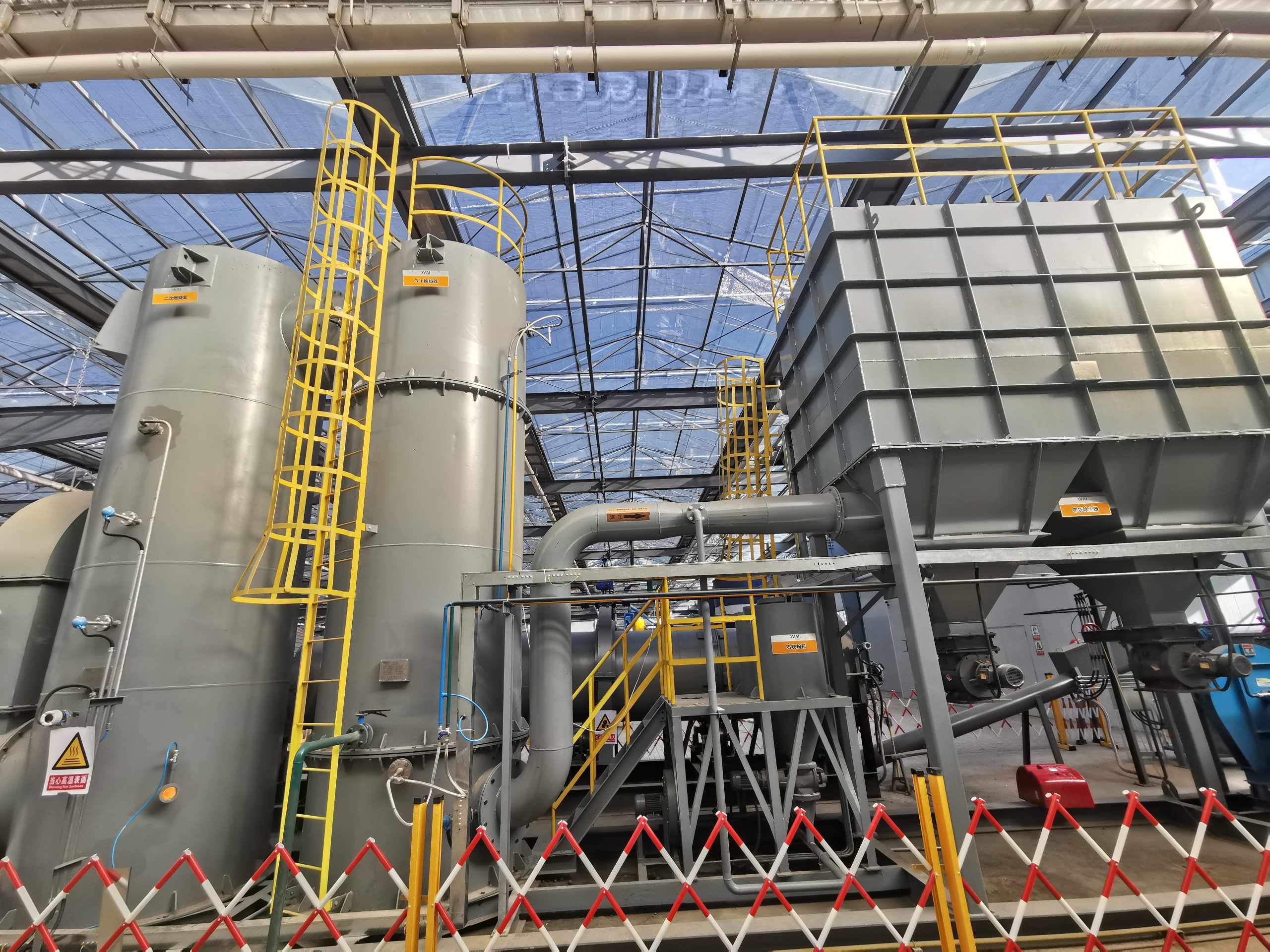
Unwavering faith in a better future
While honestly admitting that being part of the supply chain for the metallurgical industry is extremely demanding, Mr. Danielsen, Dr. Xin and their team are firmly staying on the sustainable path. Highlighting their belief in contributing to the overall decarbonisation agenda, WAI is strongly committed to being open about their manufacturing steps.
“In Norway, we have a long tradition of clean energy, some even consider it the green battery of Europe. We want to support our metallurgical industry in any way we can. Our solution and technology confirm that decarbonisation is of utmost importance to us in the long run,” Mr. Danielsen commented. “Most of my professional life was spent in the cruise industry where I was intent on doing my part to make those ships sustainable in terms of discharge of waste to the marine environment. Around twenty years ago I started working on pyrolysis for the marine industry. We are now trying to continue this on land. On a personal level, I strongly believe in valorizing waste and directing it to recycle and reuse instead of letting it pollute our planet. Therefore, I find the business we are in today very interesting to deal with.”
Dr. Xin shares his colleague´s feelings. “When I was working in environmental engineering, I realized that pollution control and improving our environment are great tasks. When starting this company in 2017, decarbonisation proved to be the main trend that motivated us to make a shift from pollution control. However, I would like to emphasize that we want to go beyond decarbonisation. Our goal is to manufacture a material that has its function and value. We are actively converting WAI from an ESG (Environmental, Social and Governance) company to an ESG material-based technology company. The steel industry offers a lot of space for advancements, and we are positive that we can make a difference.”