The future of steel production is increasingly leaning towards sustainable technologies, with a significant focus on electric arc furnaces (EAFs) and direct reduced iron (DRI) processes. As the global steel industry strives to reduce its carbon footprint, EAF technology, which largely uses steel scrap as feedstock, is expected to gain more prominence. These furnaces are more energy-efficient and produce lower CO2 emissions compared to traditional blast furnace methods. The shift towards EAFs is especially critical in regions like Europe, where stringent environmental regulations and decarbonisation targets are driving the adoption of greener technologies. Additionally, advancements in EAF technology, such as improved energy efficiency and better control over the quality of the steel produced, are likely to enhance the viability and competitiveness of this method in the coming years.
Before adopting newer technologies, many companies have more immediate targets to increase their recycled content. Recognising this demand, Tata Steel has launched its ‘Zeremis Recycled’ product with a mass-balanced recycled content of 30%. This specific percentage was chosen because Tata Steel deems it technologically feasible with their current production base. This initiative allows customers to increase their product-level circularity whilst simultaneously reducing their company-level scope 3 emissions. Tata Steel sees this as an intermediate step before transitioning to their chosen new technologies; the aforementioned EAF and Direct Reduced Iron (DRI).
DRI technology is poised to play a crucial role in the future of steelmaking, particularly in the transition towards lowcarbon steel production. DRI processes use natural gas or hydrogen instead of coal, resulting in significantly lower CO2 emissions. As hydrogen production becomes more cost-effective and scalable, DRI technologies could become a cornerstone of carbonneutral steel production. Innovations in this area, including the development of hybrid systems combining DRI with EAFs, are expected to accelerate the decarbonisation of the global steel industry. The adoption of these technologies will be pivotal as the industry seeks to balance growing steel demand with the need to minimise environmental impact, paving the way for a more sustainable and resilient steel sector.

The role of steel scrap in the circular economy
Steel scrap plays a crucial role in the circular economy by retaining material value and preventing waste, particularly of valuable alloying elements. Unlike other materials that may lose value when recycled, steel scrap maintains its worth due to its intrinsic properties and the efficiency of the recycling process. By using high-quality scrap in local high-quality steel production, the industry ensures that these alloying elements are not lost in low-value applications but are instead reintroduced into high-end steel products. Retaining and upcycling the steel scrap is one of the main drivers for Tata Steel Nederland to improve its circularity. Compared to other parties in the markets this is a distinct difference. It is important not to use high-quality scrap in low end steel applications as this lets the value of the alloying elements go to waste.
Furthermore, steel scrap is easily collected and sorted, making it an accessible and sustainable resource that supports the steel industry’s commitment to reducing environmental impact while maintaining economic viability. For this reason, Tata Steel Nederland focuses on long term relationships with its customers. Together with their customers they have set up both open and closed loop recycling initiatives. These aim to increase circularity throughout the steel value chain.
Policy and regulatory frameworks supporting circularity in steel
Government policies and regulatory frameworks play a pivotal role in advancing circularity within the steel industry, particularly in the European Union. One significant measure is the revision of the European Waste Shipment Regulation (WSR), which came into force in May 2024. This legislation imposes stricter burdens on EU scrap exporters, with a focus on restricting exports to non-OECD countries unless they meet stringent EU waste treatment standards. Larger EU countries, with greater scrap supply, have supported these stricter export restrictions to ensure that high-quality scrap, containing valuable alloying elements, remains within the EU for domestic recycling and steel production. These regulations not only support the local economy but also align with broader sustainability goals by reducing the environmental impact associated with longdistance scrap transportation and encouraging the reuse of materials in high-value applications within the region. In addition to the increasing legislative influences, there has also been a rise in the number of classification systems. One example is the recently published Low Emission Steel Standard (LESS) by the Wirtschaftsvereinigung Stahl. This particular classification system raises an interesting debate: should steel decarbonised through increased scrap use be valued at the same level as steel decarbonised through other means? The LESS classification itself (see image on page 36) sets stricter decarbonisation requirements for steel with a high recycled content.
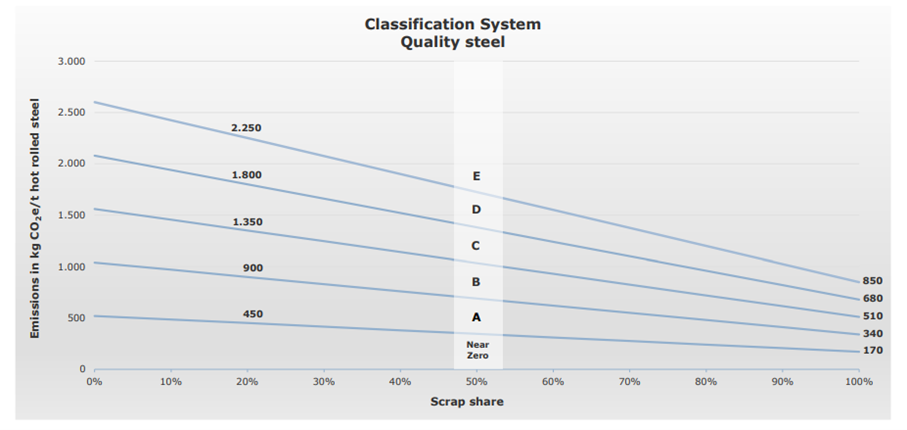
European scrap will be more difficult to export whilst being more in demand locally
Looking ahead, the European steel scrap market is expected to face increasing pressure as the region
continues to shift towards more sustainable production methods, particularly through the adoption of electric arc furnace (EAF) technology. The demand for high-quality, lowresidual scrap is likely to grow significantly, driven by the EU’s decarbonisation goals. However, supply constraints, especially for premium-grade scrap, may intensify due to tighter regulations on scrap exports under the revised Waste Shipment Regulation. These factors could lead to a more competitive market within Europe, where steelmakers might struggle to secure sufficient high-quality scrap to meet their production needs.
Globally, the competition for steel scrap is poised to intensify as emerging markets like Turkey, India, and China continue expanding their steel production capacities. With Europe potentially retaining more of its scrap supply, other regions may face tighter markets, driving up prices and encouraging investment in local recycling infrastructure. Additionally, trade policies, environmental regulations, and the evolving dynamics of global supply chains will play critical roles in shaping the availability and cost of steel scrap, with significant implications for both regional and global markets. As a result, stakeholders in the steel industry will need to navigate a complex landscape of regulatory changes, supply constraints, and shifting demand to ensure sustainable growth.
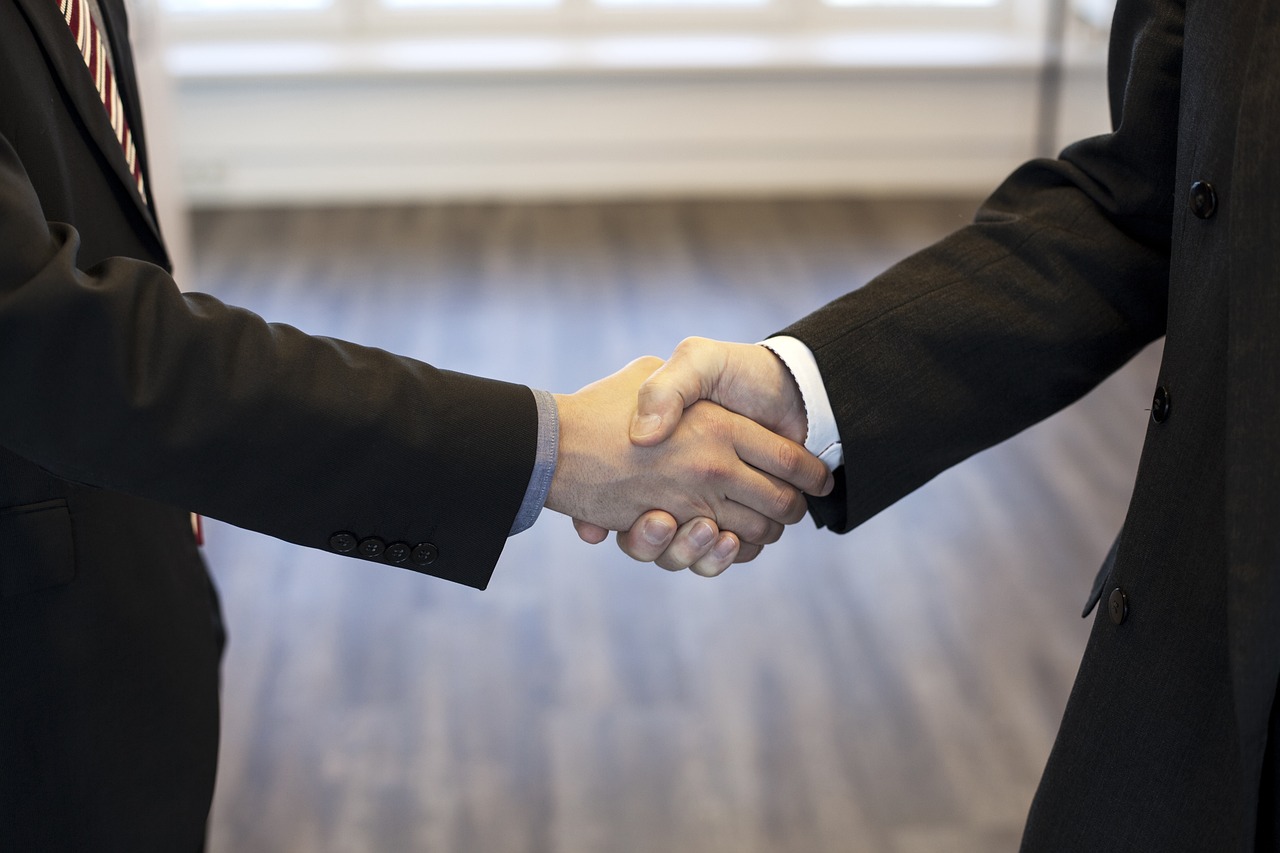