As a process specialist company in the steel, environment and energy sectors, including the design, engineering, manufacturing, installation, commissioning and start up of plants, Sarralle strives to offer its clients the optimization of their production processes, while at the same time honouring their sustainability agendas. The most recent company to put its trust in Sarralle was ArcelorMittal. The company´s team recently put into operation the world´s first 100% green hydrogen ladle preheater for ArcelorMittal Sestao. Green Steel World sat down with Dr. Itsaso Auzmendi-Murua, Hydrogen Business Line Manager, to discuss this important milestone and the company´s existing solutions as well as other projects and technologies that are on the horizon.
By Lucija Kozina
Here are the excerpts from the interview.
Another successful project under the belt
Sarralle has recently put into operation the world´s first ladle preheating station capable of running entirely on green hydrogen. The ladle preheater was an existing piece of equipment that operated with natural gas. The project consisted of improving the efficiency of the equipment by installing a new oxy-combustion burner technology which operates normally with 100% natural gas, 100% hydrogen, or blends of both gases.
I would like to highlight the trial campaign performed by Sarralle in collaboration with ArcelorMittal as an important phase of the project. In this phase, several heating and drying curves have been carried out by operating the ladle preheater with 100% green hydrogen, in order to ensure that the new equipment can satisfactorily reproduce all the required temperatures for ladle casting, achieve homogeneous heating of the refractory and that it has no negative impact on the refractory material. Seeing as the steelmaking plant does not have a continuous hydrogen supply at the moment, the green hydrogen for the trials was supplied by NipponGases and transported by semi-trailers.
It is important to stress that safety was our top priority during the project. Due to the fact that hydrogen was used as a fuel within the steel plant for the first time, safety procedures were put into place, H2 detection sensors and individual portable sensors were installed and ATEX studies were conducted.

Oxy-combustion burner technology to the rescue
Currently, most high-temperature heating equipment in the steel industry operates with natural gas as fuel and air as an oxidizing agent. Disregarding water vapor, atmospheric air contains around 79% nitrogen and only 21% oxygen. Therefore, during the air combustion process, nitrogen must be heated, losing process efficiency. Seeing as the nitrogen component is not heated during oxy-combustion, fuel consumption is reduced.
The transition from the traditional operation with natural gas and air to oxy-combustion results in fuel savings of between 10-50% depending on the current operation of the equipment, with consequent reduction of CO2 emissions. For instance, for ladle preheaters, a natural gas consumption reduction of 50% is obtained with a subsequent decrease in OPEX costs. The introduction of hydrogen as a fuel will mark an even greater reduction in CO2 emissions, making the goal of zero CO2 emissions highly achievable.
Oxy-combustion technology allows for a more efficient use of green hydrogen compared to that of air combustion. Given the technological and social challenges associated with the green hydrogen production increase that is expected in the coming years, the most efficient technology for hydrogen consumption should be applied. In fact, we have partnered with NipponGases for the design and manufacturing of oxy-combustion hydrogen burners which will enable full replacement of natural gas in industrial heating systems.
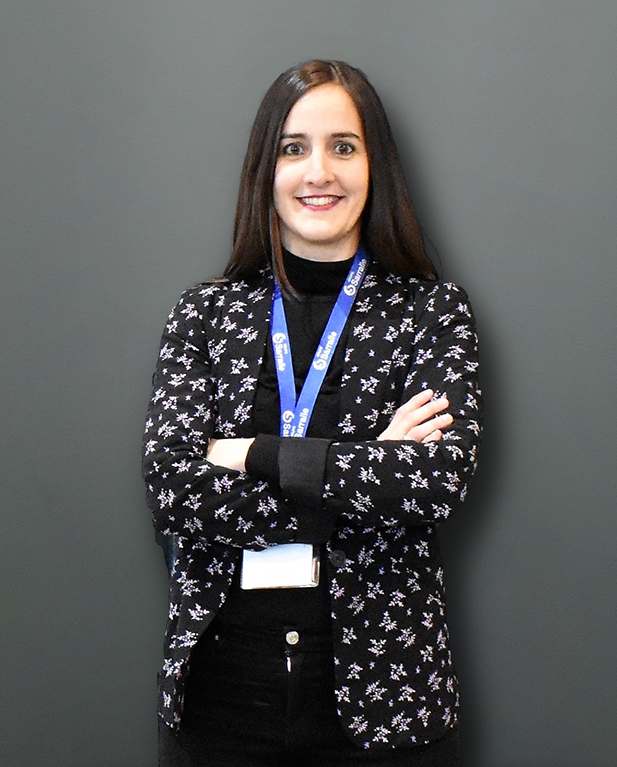
Taking emission reduction one step further
A major advantage of oxy-combustion over air-combustion is the potential for the reduction of NOx emissions (nitrogen oxides, NO and NO2). Thermal NOx refers to the NOx formed through high-temperature oxidation of the nitrogen found in the combustion air. Since oxy-combustion uses pure oxygen as the oxidizing agent, there is almost no nitrogen present in the combustion process, therefore, NOx are not formed. When oxy-combustion technologies are applied, the only NOx formation comes from infiltration of air in and around the equipment, along with some N2 that can be present in both the natural gas and oxygen. The ladle preheater project included the measuring of the exhaust gases, in order to confirm the reduction of CO2 and NOx emissions.
A positive attitude is valid but strong collaboration remains key
Steelmakers are initiating industrial testing of their heating equipment within the framework of hydrogen-based use, which is the most important step. The positive results obtained in the trial campaigns performed at the ladle preheater confirm that it is feasible to operate this heating equipment with 100% hydrogen.
It is worth mentioning that the burner technology used for the ladle preheater is also applicable to other heating equipment such as Tundish preheaters and reheating furnaces. We have also adapted our Blue Efficient Arc Furnace to the newly developed H2 injector. Sarralle is already involved in the industrial implementation of these solutions.

Our focus is currently on working with a close customer to convert a reheating furnace into oxy-combustion burner technology, which will also be able to operate with both natural gas and hydrogen. Reheating furnaces consume around 75-80% of natural gas of the entire steelmaking plant and are therefore responsible for the largest portion of the facility´s CO2 emissions. Improving the efficiency of the reheating furnaces via oxy-combustion and taking a step further to operate them with 100% hydrogen will allow the almost complete decarbonization of EAF-based plants.
The decarbonisation of the steel industry requires significant technological and social advancements. The conversion of the equipment to both a new fuel and oxidizing agent results in significant changes which must be studied in detail. To overcome these challenges, in Sarralle we have set ourselves the strategic objective of making a coordinated effort together with technology centers, experts in hydrogen generation, and steel companies. We strongly believe that collaboration between different entities is the key to the goal of making a net zero CO2 emission steel industry a reality in the near future.
No rest for the steel industry shareholders
HyInHeat is a European-funded project and one of the largest consortiums that are working on the topic of integrating hydrogen technologies industrially in the steel industry. It is based on the collaboration of 30 partners from 12 countries. Within this project, Sarralle is working on converting the combustion system of an existing industrial walking beam reheating furnace, from natural gas and air combustion to 100% hydrogen oxy-combustion.