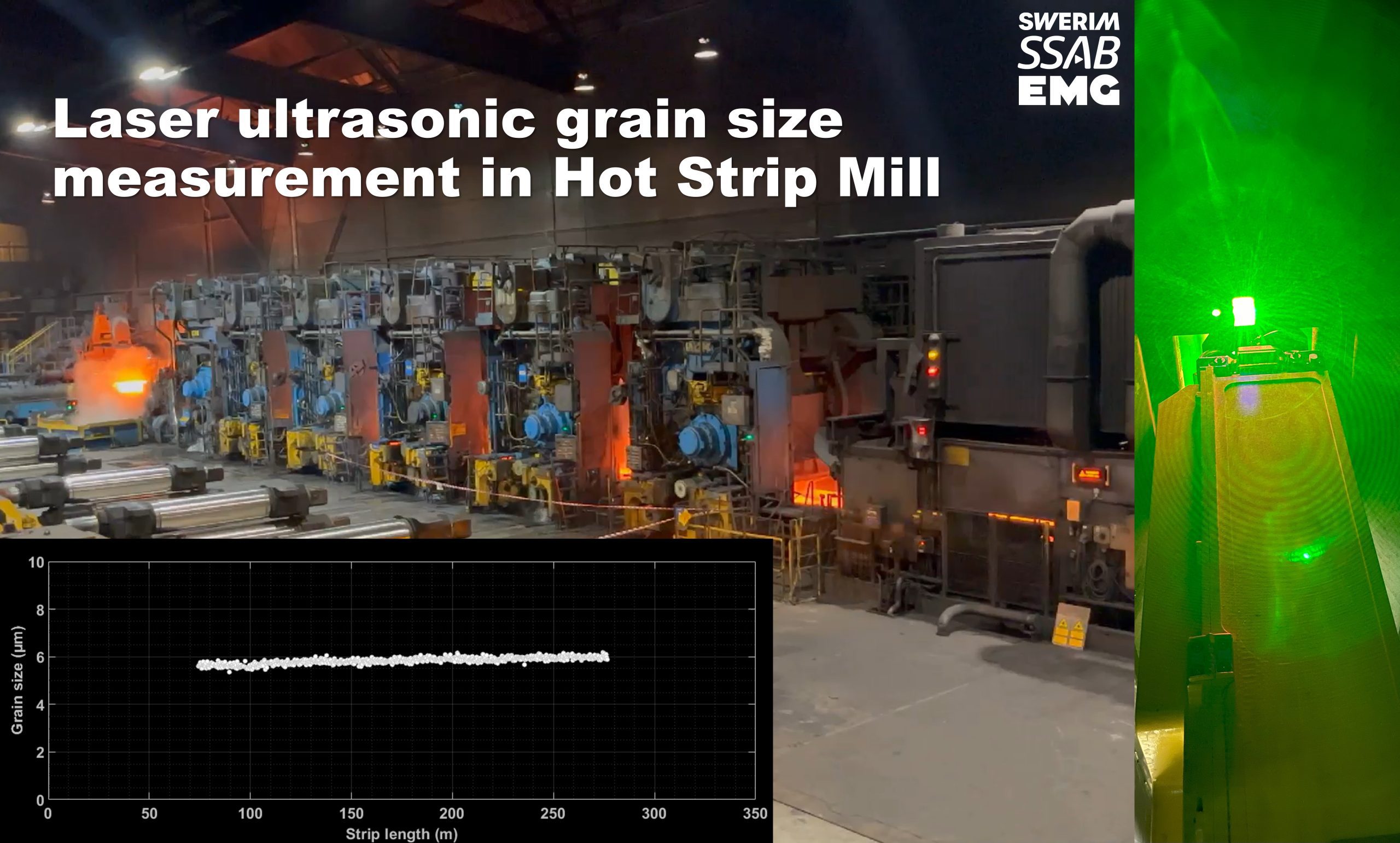
By Mikael Malmström, Swerim
Understanding the basics: What is laser ultrasonics?
Laser ultrasonics is a non-contact measurement technique that uses lasers to generate and detect ultrasonic waves in materials. In simple terms, it involves firing a short laser pulse at the surface of a material to create ultrasonic waves, which then travel through the material. Another laser then detects the response of these waves, allowing scientists to analyze the material’s properties and microstructure. A schematic illustration of the ultrasonic measurement principle is given in Figure 1 below.
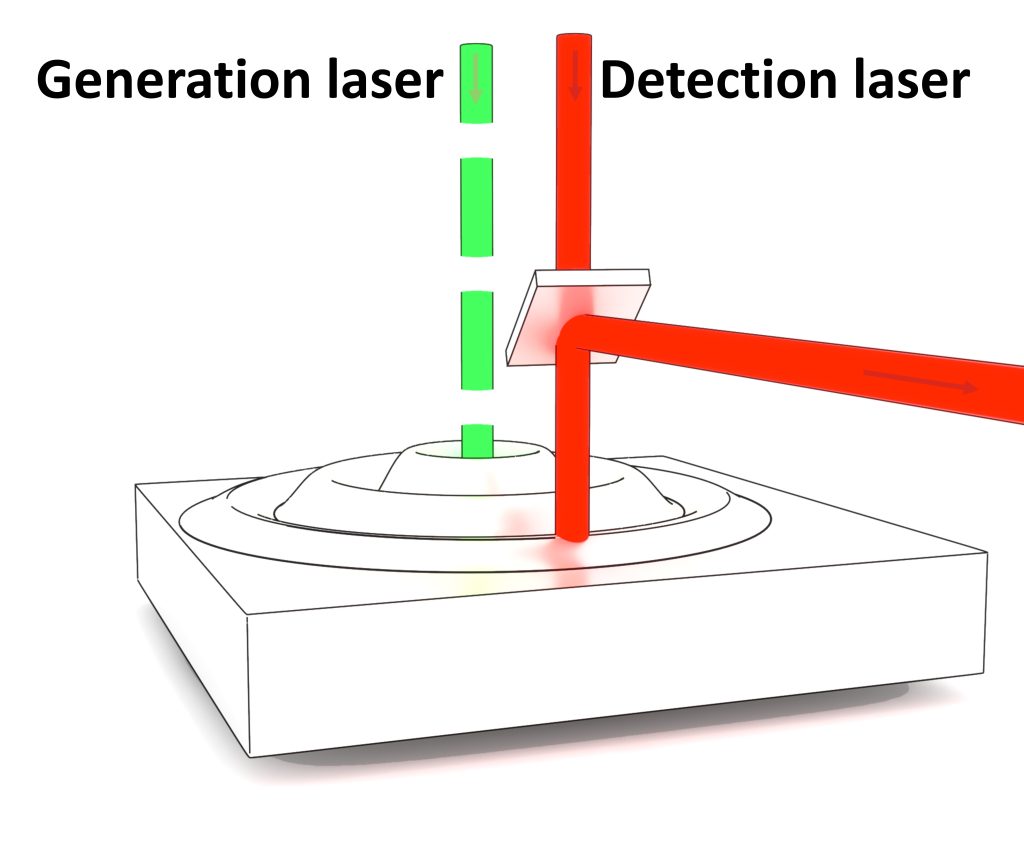
The process begins with a short-pulsed laser, known as a Q-switched laser, which generates the ultrasound by creating a plasma on the material’s surface. This plasma causes a thermal expansion that generates an ultrasonic shockwave. The response of the ultrasonic wave is then measured by analyzing the Doppler shift of the surface reflection using another laser. This technique, developed in the 1980s and 1990s, has been commercially employed in the metal industry since early the 2000s for monitoring wall thickness during the production of seamless steel tubes.
The game-changer: LUS-based grain size gauge
The new LUS-based grain size gauge represents a significant leap forward in steel production technology. Installed in the hot strip mill at Borlänge, Sweden, this system is the first permanent setup to monitor the microstructure of steel during hot rolling. The gauge is positioned after the last stand and before the run-out table, ensuring it captures critical data during the production process.
One of the key features of this gauge is its ability to measure the grain size of steel in real-time. Grain size is a crucial factor in determining the properties of high-strength steel and other types of steel. Traditionally, measuring grain size during the hot rolling process has been challenging due to the extreme conditions, with temperatures ranging from 800-1200°C and material moving at speeds of up to 10 m/s. The LUS-based grain size gauge is the only technique to overcomes these challenges, while providing accurate and reliable measurements.
How it works: Simplified explanation
The LUS-based grain size gauge operates by analyzing the frequency-dependent attenuation of ultrasonic waves as they pass through the steel. Here is a simplified breakdown of the process:
- Generation of ultrasound: A laser pulse hits the surface of the steel, creating an ultrasonic shockwave.
- Detection of response: Another laser detects the response of the ultrasonic waves that travels inside the steel.
- Frequency analysis: The system analyzes the frequency-dependent attenuation of these waves. Higher frequencies are attenuated more than lower frequencies, and this attenuation is related to the grain size of the steel.
- Grain size calculation: Using a calibration curve, the system translates the measured attenuation into an average grain size value.
This method allows for real-time monitoring of the steel’s microstructure, providing valuable data that can be used to optimize the production process.
Impact on the green steel transition
The introduction of the LUS-based grain size gauge is particularly significant in the context of the green steel transition. As the industry moves towards more sustainable practices, there is a growing emphasis on using scrap-based and hydrogen-reduced steel. These new methods aim to reduce the carbon footprint of steel production, but it is crucial to ensure that the resulting steel has the same properties as traditional steel made from iron ore.
The LUS-based grain size gauge plays a vital role in this verification process. By providing accurate measurements of the steel’s microstructure, it ensures that the new, greener steel meets the required standards. This capability is essential for gaining industry acceptance and driving widespread adoption of sustainable steel production methods.
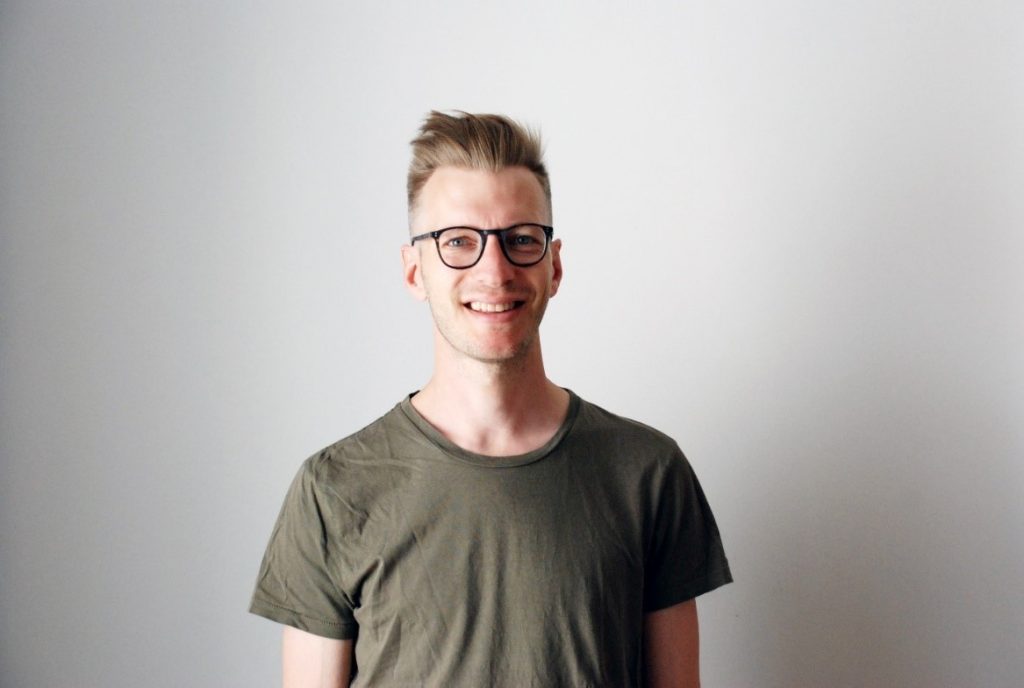
Real-world applications and benefits
The LUS-based grain size gauge has already been installed and tested in the SSAB mill in Borlänge, Sweden. The system has demonstrated its ability to provide reliable measurements in the harsh environment of a hot strip mill. The gauge’s robust design includes optics for a long working distance of more than half a meter and suitable protection against the harsh conditions.
In practical terms, the gauge offers several benefits:
- Enhanced quality control: By monitoring the grain size in real-time, the gauge helps identify deviations in the production process, allowing for immediate adjustments and ensuring consistent quality. For some steel grades the Hall-Petch relation can also be utilized to measure the mechanical properties without need for destructive testing. Hence, facilitating mechanical data over the entire length of the strip/coil without the need for costly and time consuming destructive testing while at the same time increasing the yield.
- Process optimization: The data collected by the gauge can be used to optimize the production process, in both feed-back/forward control loops as well as assisting the setup calculation in between strips leading to more efficient and cost-effective production.
- Accelerated material development: The real-time and detailed microstructure data provided by the gauge can be used to develop new alloying concepts and to improve existing materials, and materials models, thus accelerating the pace of innovation in the steel industry.
Conclusion
The new LUS-based grain size gauge is a groundbreaking technology that has the potential to revolutionize the steel industry. By providing real-time, accurate measurements of the steel’s microstructure, it supports the transition to greener production methods and ensures the quality and consistency of the resulting steel. As more steel companies adopt this technology, we can expect to see significant advancements in both the efficiency and sustainability of steel production.