Modern human life as we know it would be deemed unimaginable without steel. The metal plays a vital role in more aspects of our lives than we are possibly aware of. So, the bottom line is that we can’t stop using steel. But the traditional and still widely used method of steel production is majorly polluting the planet. So how do we move forward? The good news is that there is a sustainable way. Swiss Steel Group owing to its expertise in recycling, electric arc furnace technology and the highest operating standards, has already been able to reduce the carbon footprint of its products to well below the industry average. But it strives to further reduce its environmental footprint until the Swiss Steel Group name stands for climate-neutral steel.
For the uninitiated, a white paper is a report or guide that informs readers concisely about a complex issue and presents the issuing body’s philosophy on the matter. Swiss Steel Group has published a white paper, covering a wide range of topics, giving a detailed explanation of why the ecological footprint of Swiss Steel Group is almost 78% lower than the industry average worldwide and how it plans to become even more environmentally friendly in the future.
By launching the Green Steel initiative, Swiss Steel Group aims to not only become a global industry leader but also empower its customers to make well-informed choices with high-quality sustainable products and fully transparent carbon reporting. And here is how the company headquartered in Lucerne, Switzerland, plans to achieve the gargantuan task.
Adopting the electric arc furnace route
While the majority of the world’s steel is being produced using the blast furnace route, Swiss Steel Group pursues exclusively the electric arc furnace route. The EAF process is capable of producing all types of steel with a relatively smaller and far more efficient set up. The raw material used in an EAF is usually steel scrap and the main source of energy is electricity. This process requires fewer energy-intensive intermediate stages that the BF route and managing the temperature within the system is even relatively easier.
Nevertheless, the EAF route does come with its fair share of challenges.
Green electricity is an issue that the steelmaker has already confronted by switching to electricity provided by hydropower at Steeltec, the Group’s Swiss plant located in Emmenbrücke.
Figuring out scrap logistics is an arduous task and is expected to become all the more complex in the future. The available scrap volume is not always the same, and highly sought-after quality scrap, needed to produce a precise steel grade is often lacking and needless to say, expensive.
Nota bene: The Switzerland location is not the only Group site using renewable energy. The steel mill in Canada and bright steel production in Düsseldorf, Germany are also producing steel entirely with electricity from renewable sources. Production in Germany and France is also switching to renewable energy to meet customer demands.
Hydrogen in, natural gas out
It is widely accepted that the next step of the global energy transition will be based on the hydrogen economy and Swiss Steel Group is also focussing on replacing natural gas to heat steel before rolling. The steelmaker plans to use hydrogen eventually but synthetic gases in the meantime. But there are some challenges in pursuit of a green transition.
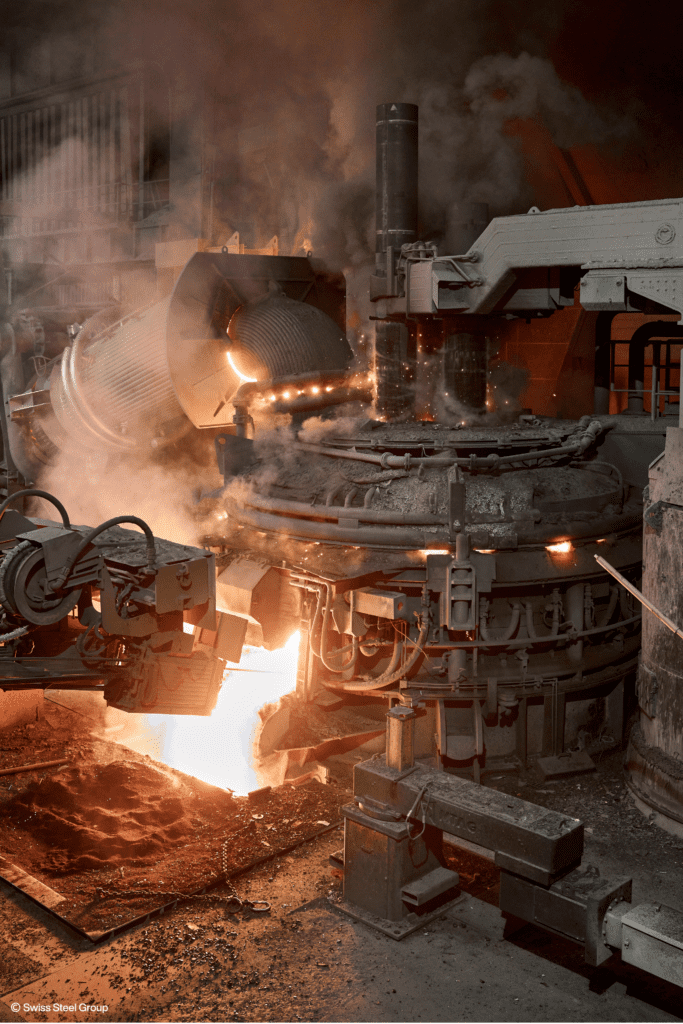
The supply of green hydrogen is far below the levels required to induce the net-zero scenario and the costs are significant and unviable from a commercial perspective, at this point in time.
Additionally, the use of hydrogen in the steel industry also presents several technical challenges like maintaining the correct volume ratio when hydrogen is mixed with natural gas, hydrogen-induced brittleness in steel, etc.
Notwithstanding, according to the white paper, Swiss Steel Group makes sure that its processes now already need as little natural gas as possible, and in future even fewer synthetic gases. At the same time, it is important to establish an active presence in the political and public spheres. What are needed are the general conditions and economic stimuli to make these gases available in the necessary quantities.
Green power
As already mentioned, the Swiss Steel Group plant in Emmenbrücke only uses electricity supplied by Swiss hydroelectric power stations. However, Switzerland is at risk of a power shortage triggered not by a lack of electricity, but by a lack of transport capacity.
As of 2025, 70% of the transmission capacity of the grid in the EU is reserved for power trading within the region. If no agreement with the EU can be put into place by then, the power shortage would hit the big consumers first – and thus also the Swiss location of Swiss Steel Group.
Because even though the production sites in Switzerland exclusively source local green electricity, the lack of coordination with Europe and above all the lack of imported electricity can cause the grid to become unstable.
The white paper clearly states that decarbonisation must go hand-in-hand with political engagement that ensures that industries that take the fight against climate change seriously are not put at a disadvantage.
Quality scrap trumps alloying metals
According to the World Steel Association data, 70% of the steel produced till date is still in use and recycling scrap instead of virgin materials reduces CO2 emissions by 58%. To put things in perspective, recycling one tonne of steel can avoid the release of 1.67 tonnes of CO2, which means 86% less air pollution.
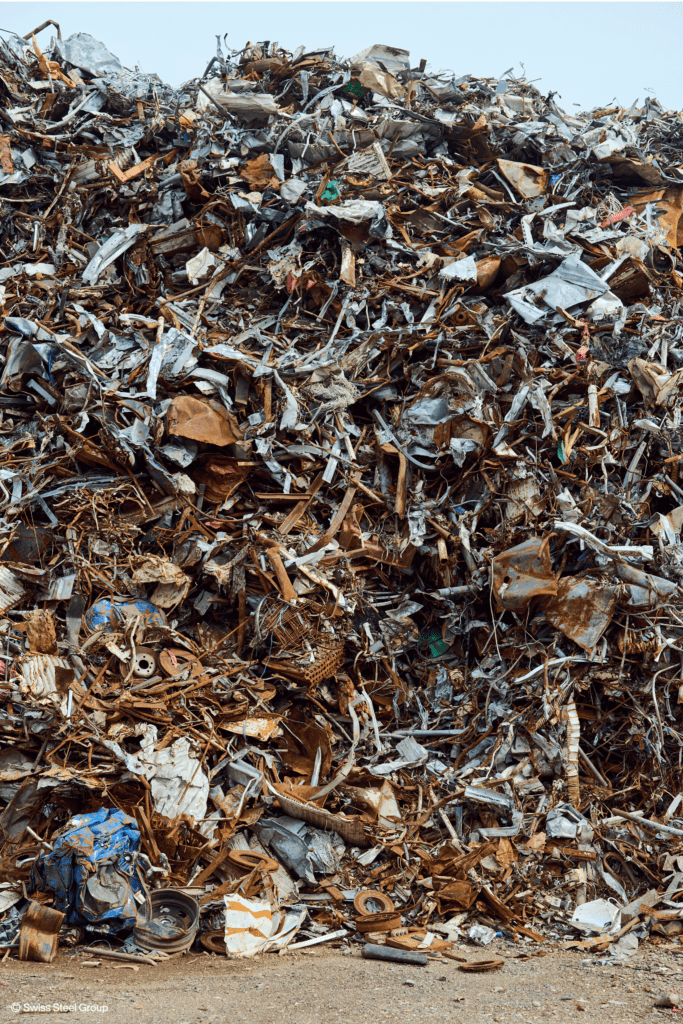
As per the white paper, it is important in the future both for ecological as well as political reasons to rely more on quality scrap for alloying instead of pure metals.
Swiss Steel Group has already managed to reduce the carbon footprint by switching from pure primary alloys such as ferrochrome, ferronickel, ferromanganese, or ferromolybdenum to high-alloyed scrap in the production of high-alloyed and stainless steel.
But it goes without saying that guaranteeing consistently high quality in the steel melt with scrap is much more difficult than if a pure material were used.
Recognize, act, inspire
There are a total of three scopes in which companies emit CO2.
Scope 1: comprises a company’s direct CO2 emissions.
Scope 2: comprises the indirect CO2 emissions by energy suppliers.
Scope 3: comprises the indirect CO2 emissions of the upstream and downstream supply chain.
Swiss Steel Group not only assumes responsibility of empowering its customers, but it also plans to maintain a competitive edge by being transparent about its carbon emissions reporting.
Swiss Steel Group plans to record the data and emission values of Scope 1, Scope 2 and Scope 3 and then pass the numbers on to its customers and put them in a position of determining their own carbon footprint.
Circular economy pioneer
It is a well-established fact that steel is ubiquitous, necessary, and highly versatile. But it also has another outstanding characteristic: it can be endlessly recycled.
In the case of low alloy steel recycling, the material qualities do not get compromised but Swiss Steel Group has found a way of reclaiming alloying elements such as chromium, nickel, or molybdenum from highly alloyed steels with reduced energy input.
The Swiss Steel Group company Ugitech in France aims to produce primary alloys from waste products such as batteries, catalytic converters, and similar products under its project named Ugi’Ring.
Thanks to Ugi’Ring process, Swiss Steel Group’s new products are of higher quality than the original scrap – and recycling has actually become upcycling.
In a nutshell
The eight-page detailed report released in June 2022 heavily focusses on Green Steel’s role as a research and technology platform. It also highlights Swiss Steel Group’s elaborate plans of using the waste heat as a resource and an important area of research. According to the white paper, the company also believes that the steel industry’s green transition will set a great example for other industries to follow.
Moreover, through Green Steel, Swiss Steel Group sends out an invitation to business partners, researchers, authorities, and external organisations to decarbonise the economy together.
Read Swiss Steel Group’s White Paper here: https://www.swissgreensteel.com/