AST’s roots stretch back to 1884 when Terni entered the annals of steelmaking history. The town became home to the monumental industrial complex known as “Società Alti Forni, Fonderie e Acciaierie di Terni” (SAFFAT), marking a pivotal moment in Italy’s industrial landscape. In 2022, Arvedi acquired AST Terni, signaling a signicant investment aimed at both expanding production capacity and advancing decarbonisation efforts through the principles of the circular economy.
This strategic acquisition not only bolstered the Arvedi Group’s position in primary stainless steel production but also paved the way for future growth opportunities. Leveraging synergies within the group, Arvedi AST now boasts 140 years of expertise, positioning itself as one of the leading integrated steelmaking facilities in Europe, specializing in stainless-steel at products at its fully integrated production plant, which produces one million tons annually. Additionally, the company’s Forgings Division ranks among the world’s largest producers of special steel forgings, while its subsidiary, Tubicio di Terni, manufactures electro-welded stainless-steel tubes.
Arvedi Group´s structure and portfolio
Today, the Arvedi Group, notable for its operations in both the carbon steel and stainless steel industries, encompasses a spectrum of operations. These include the production of hot and cold rolled carbon and stainless-steel coils, carbon and stainless-steel tubes, precision re-rolling of stainless-steel strips, and steel product trading. Each company within the group is meticulously crafted for specialization, boasting optimized production processes, state-of-the-art technology, and in-house operational practices geared towards enhancing efficiency, quality, and flexibility.
“In addition to our core specialties, we are proud to hold a significant presence in the European market for corrosion-resistant pipes, led by another company in the stainless steel business, Ilta Inox. Furthermore, Arvedi stands as a major global player in the production of stainless steel precision strips, with the company Arinox leading the charge. Arinox produces a substantial volume of precision strips, with a predominant focus on export, accounting for 85-90% of total production. The precision strips find applications across a wide range of industries, catering to diverse markets and customers with varying quality, service, and sustainability requirements. From automotive to heat exchangers, electronic and biomedical sectors, to precision engineering, Arinox´s products serve an array of critical applications,” Mr. Gigli explained.

Chief Technical Officer at Arvedi AST
Arvedi Group is at the forefront of the sustainability issue, so much so that in July 2022 it obtained the international “net zero emissions” certification, making Acciaieria Arvedi’s Cremona and Trieste plants the first in the world to be carbon neutral with fully compensated CO2 emissions. A result that makes the Arvedi Group a point of reference for sustainability in the iron and steel industry.
Under the guidance of highly skilled management, the organization of the entire Group operates with agility and precision, ensuring maximum production and quality efficiency while providing exceptional service tailored to evolving market demands. Through strategic technological and ecological decisions, the group maintains a steadfast commitment to people and the environment, operating in harmony with both.
Path towards decarbonisation
“Aligned with our mission of achieving carbon neutrality, Arvedi Group is at the forefront of implementing disruptive technologies for steel production. Arvedi Endless Strip Production (ESP) technology stands as a testament to this commitment, revolutionizing carbon steel production by significantly reducing both costs and environmental impact. Arvedi sets the benchmark in the market with a carbon footprint of 133 kilograms of CO2 equivalent per ton of crude steel, inclusive of scope one and scope two emissions before offsetting with carbon certificates,” Mr. Gigli elucidated when asked about Arvedi´s sustainability agenda.
Arvedi AST, as Mr. Gigli remarked, is one of the companies that represents the Group´s responsible ways best by recognizing the urgent need for sustainability and integral development. While profitability must remain one of the objectives, it must be pursued through responsible and ecologically compatible means. This is underlined by the fact that Arvedi AST´s production facilities include two electric arc furnaces (EAFs), two AOD converters, one VOD converter, multiple ladle furnaces, and two continuous casting machines.
“We boast a comprehensive array of processing equipment, including a reversible roughing mill, finishing stands and auto-rolling facilities. Our finishing shop ensures a diverse range of stainless steel finishes, while a specialized coating line offers renowned anti-fingerprint coatings, catering to various market demands,” he highlighted.
Arvedi AST´s production process itself relies exclusively on scrap and ferroalloys as raw materials. For the production of austenitic stainless steel, stainless steel scrap is predominantly utilized, whereas carbon scrap and ferroalloys are the primary inputs for manufacturing ferritic grades.
“We maintain close relationships with a network of suppliers, ranging from key partners to local suppliers in close proximity to our facilities. This collaborative approach to supplier engagement is essential in our efforts to reduce emissions. By sharing our vision for the future and involving our suppliers in initiatives aimed at enhancing their processes and supply chains, we collectively work towards our sustainability goals,” Mr. Gigli underscored.
“The utilization of scrap holds paramount importance in our operations, with recycled materials constituting approximately 94% of our steel content – an achievement we take immense pride in. Moreover, we are actively pursuing initiatives to transition from natural gas to green hydrogen – a move aimed at further reducing our carbon footprint. Our ongoing investments, particularly in furnace upgrades and burner technologies capable of utilizing 100% hydrogen, represent a key step towards realizing this vision. While the widespread adoption of green hydrogen presents both operational and capital expenditure challenges, we view it as a promising solution for decarbonising not only carbon steel but also stainless steel production,” Mr. Gigli stated.
Moreover, the company´s focus includes research and development, exploring cutting-edge technologies like carbon capture and usage, which hold the potential to further advance their sustainability efforts. They are actively investigating innovative solutions, such as utilizing their slag as a means to trap and store CO2, in line with their commitment to environmental stewardship.

Renewables and energy efficiency
Arvedi AST’s commitment to sustainability extends to its energy usage practices. Their facility in Cremona has already transitioned to using 100% certified renewable energy, supplied by energy companies. Similarly, Arvedi AST in Terni is actively pursuing a similar transition, leveraging its strategic advantage of proximity to abundant hydropower resources. With the highest waterfall in Europe nearby, once owned by Arvedi AST, their logistical advantages enable them to expedite the adoption of renewable energy sources.
“Currently, approximately 40% of our energy usage is derived from renewable sources, with plans to increase this figure significantly in the near future. Moreover, we are investing heavily in energy efficiency measures to reduce our overall energy consumption. One notable initiative is the implementation of a new walking beam furnace for heating slabs before rolling, achieving a remarkable 40% reduction in energy consumption – a significant milestone in our journey,” Mr. Gigli emphasized.
In addition to renewable energy integration and energy efficiency improvements, Arvedi AST prioritizes water conservation through closed-loop water systems and responsible water management practices. “By utilizing a nearby river as a water source and implementing closed-loop water recirculation systems, we minimize water consumption and ensure responsible usage of this vital resource,” he explained.
Looking ahead, Arvedi AST is exploring the production of green hydrogen through on-site electrolysis, with plans to utilize this hydrogen within its operations. This approach not only reduces reliance on external suppliers but also positions Arvedi AST as a pioneer in sustainable energy production.
Furthermore, Arvedi AST is committed to promoting circularity within its operations, maximizing resource efficiency, and minimizing waste generation. Through innovative initiatives such as metal recovery from slag and dust, and collaboration with industries such as cement and asphalt, they aim to transform waste into valuable resources for secondary applications, fostering a more sustainable and circular economy.
Steadfast journey
As already mentioned and exemplified, sustainability has been a central focus of Arvedi AST since the acquisition. This commitment is evident in every aspect of the company’s operations, from reducing carbon emissions to adopting innovative green technologies. Arvedi AST continues to prioritize eco-friendly practices, ensuring that their processes, products, and overall impact align with their sustainability goals.
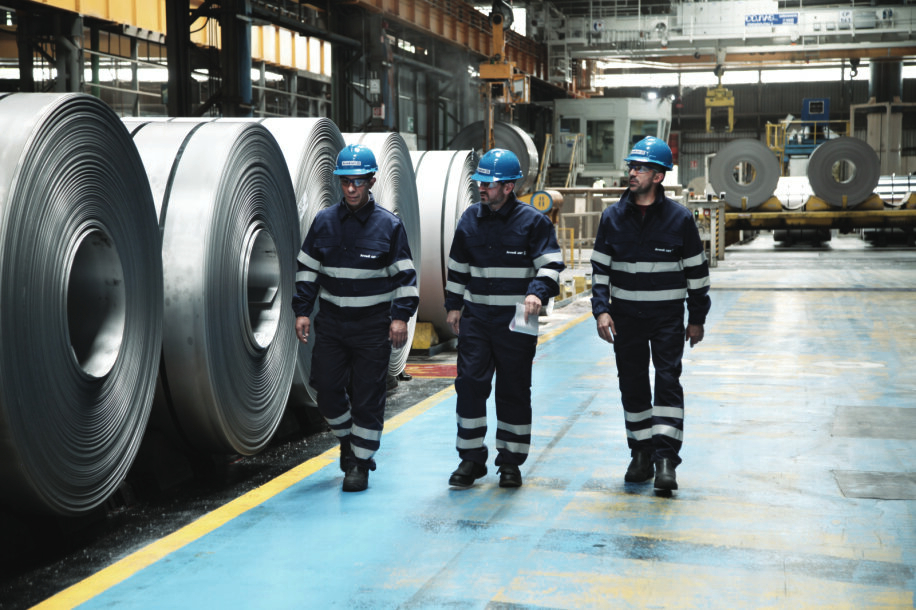
“Utilizing green steel presents a significant opportunity in our quest for sustainability. We must address the needs of our generation without jeopardizing the ability of future generations to do the same. This is not just a European priority – it is a global imperative that requires collective action,” Mr. Gigli commented on the current state of the (green) steel industry.
He brought our conversation to a close by remarking on the company´s distinctive features: “Arvedi holds a unique advantage as a family-owned business, placing a strong emphasis on stakeholder welfare, particularly the well-being of our employees and the communities surrounding our mills.”
As a further confirmation of their commitment, Arvedi AST is the latest to obtain core site certification against the ResponsibleSteel International Standard. Notably, the site in Terni is Italy’s first to receive this certification, highlighting Arvedi AST´s dedication to responsible steel production.