ANT AG specializes in Water Abrasive Suspension (WAS) technology, the development and manufacture of modular cutting systems and erosion technology. The GSW editorial team gladly accepted the opportunity to hear what Mr. Till Weber, General Manager of ANT AG, has to say about the company´s remarkable results achieved in compliance with all international requirements for sustainable ship recycling. Please read on to find out more about the abundance of potential offered by the company´s technology.
GSW: Mr. Weber, can you please tell us something about ANT AG and its (sustainability) mission?
TW: ANT AG was established in 1999 with a mission to explore sustainable cutting methods based on suspension jet technology. This endeavor led to the invention of a unique Water Abrasive Suspension (WAS) system, which has since been at the forefront of our continuous technological development.
Today, ANT stands as a market leader in cold-cutting systems for offshore decommissioning, bomb disposal and dismantling of nuclear power plants. Furthermore, we are actively extending our technology’s application to the realms of ship recycling and railway cleaning. Sustainability is deeply ingrained in our DNA, as our operations involve dismantling and recycling, relying solely on natural elements like water and abrasive (sand) for our technology’s functionality. Moreover, we use the natural power of bionics.
GSW: Please tell us more about your waterjet technology. What are some of the advantages? Are there any limitations to the type of material that can be recycled/cut?
TW: In conventional WAIS (Water Abrasive Injection System), water flows under very high pressure through the nozzle into the cutting head of the system. The abrasive is sucked into the mixing chamber by negative pressure (“Venturi principle”). This results in an air content of around 95 percent, which leads to turbulent mixing losses and severely reduces the overall efficiency of the cutting jet. In ANT WAS systems, on the other hand, part of the pressurized water flows via a bypass valve into the Abrasive Mixing Unit (AMU). Water and the cutting agent (abrasive) form a suspension there. The water abrasive suspension is directed and forced through the cutting nozzle via a high-pressure hose. The potential energy of the pressure is converted in the nozzle into a cutting jet that emerges at almost twice the speed of sound. The result is a two-phase jet consisting of approximately 97.5 percent water and 2.5 percent abrasive.
Since the abrasive particles in WAS systems are directly bound in the water, the ANT suspension jet is significantly more stable, precise, and up to three times more powerful than the injection jet. There is no air in the jet and no unwanted air bubbles are produced underwater. Due to the special ANT nozzle geometry, WAS systems do not require high pressure and consequently save resources. Regarding the material, there is no limitation, anything can be cut. We have already cut steel of one meter thickness.

GSW: Are there any regulations that stipulate clean and safe ship recycling? Is your technology sustainable?
TW: EU regulations mandating clean and secure ship recycling, such as the Hong Kong Convention and EU Regulation 1257/2013 on ship recycling, are in place. Our technology offers sustainability advantages over current cutting methods. It diminishes health hazards faced by workers who must wear extensive safety equipment during cutting processes, while also minimizing air and sea pollution. In addition, we are also offering an abrasive recycling unit to reuse the abrasive used in the cutting process. In contract manufacturing, for example, you can use our abrasive recycling unit and reprocess the abrasive. While dismantling offshore structures, such as offshore oil rigs, most of the cutting process takes place below the sea surface. Therefore, the water we use will go back to its original source as well as the abrasive.
GSW: Can you please comment on the quality of the material being recycled? Is there any loss of quality or change in quality?
TW: The quality of the material being recycled with the WAS technology is superior compared to the current cutting technologies. As it is a cold process, no toxic slag or fumes are produced. Furthermore, it is more predictable as it does not rely on the quality of the worker. In addition, we can cut from outside to inside which makes it easier to recycle used water and abrasive.

GSW: If I am not mistaken, you provide shipyards with your technology as a tool. Can you please elaborate on some projects you are participating in?
TW: We have two primary approaches: either we provide our technology, and a partner seamlessly integrates it into a manipulation system, like a robot; or we offer an all-inclusive solution. It is worth noting that ship recycling is still in its developmental stages in Germany. A significant portion of recycling occurs in Southeast Asia. We are proud to contribute to ship recycling and the production of environmentally friendly steel. The first pilot projects with our technology are underway in Germany.
GSW: The availability of scrap is one of the problematic points of the steel industry. With regard to ship recycling, how much scrap potential is there?
TW: Super large vessels were built just two to three decades ago, and the earliest of them are approaching their recycling phase. As a result, we perceive substantial potential within this industry, albeit with regional disparities. We foresee Southeast Asia maintaining its dominance in the recycling of large vessels, while the European market is likely to shift its focus towards smaller vessels.
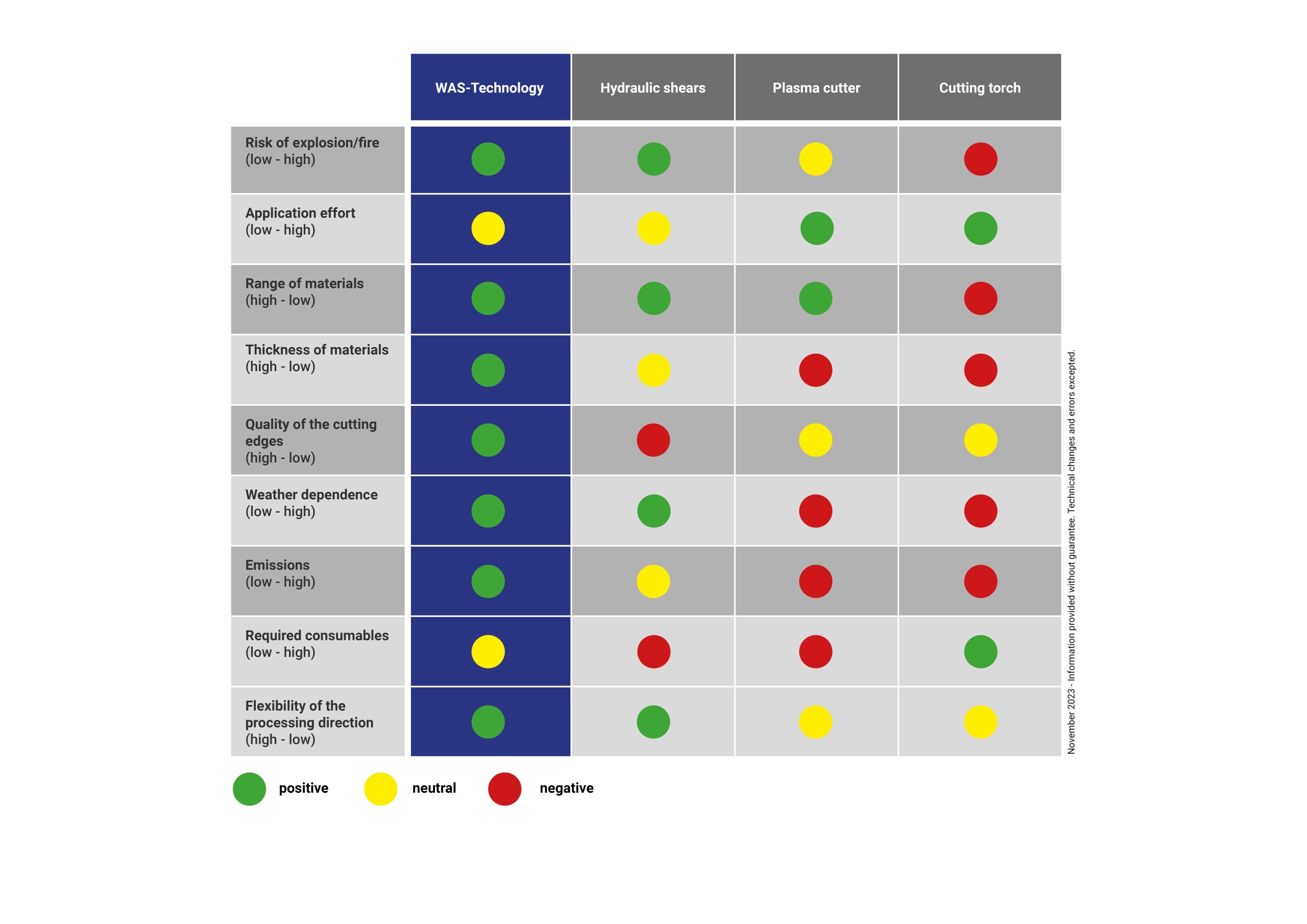
GSW: Is ANT AG active worldwide? Where do your operations mainly take place?
TW: Our headquarters is in Lübeck, and we are set to establish a new branch in the UK by 2024. Given our clientele’s global reach, we maintain an extensive sales and service network worldwide. I am proud to say that our team of more than fifty good-minded and internationally oriented people is successfully building up this network.
GSW: Do you perhaps plan to apply your technology somewhere else in the industry aside from recycling ships?
TW: Our technology serves diverse purposes, from bomb defusing, wind farm installations dismantling and decommissioning of oil & gas rigs off- and onshore to ongoing testing for the removal of leaves and vegetation from railway tracks. Furthermore, we have established a
subsidiary company, ConSus GmbH, dedicated to continuous waterjet cutting, allowing for advancements in the water jet cutting industry.
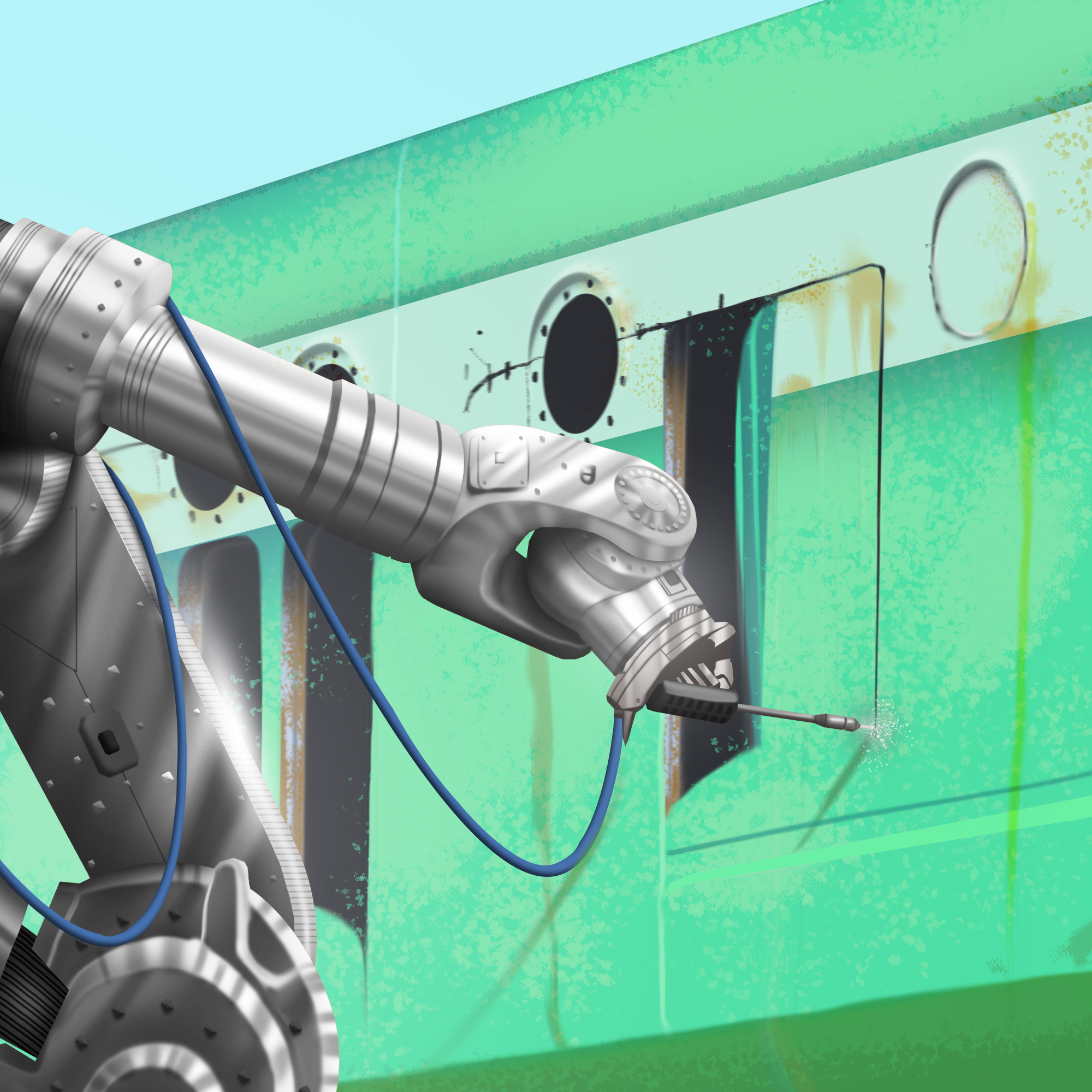
GSW: Do you have any predictions for the ship recycling industry? Do you see it becoming more sustainable in the future?
TW: That is a very difficult question. It is worth noting that around 15 thousand ships with a total transport capacity of 600 million tonnes are to be recycled in the next decade. This will allow for industrialization of the ship recycling business. Current technologies that are being used in some parts of the world generate significant amounts of CO2. In Europe, there is a lot of pressure for emission reduction. On an international level, much more needs to be done in order to get all the stakeholders on board with the sustainability plans. I believe that all parties included (ship owners, yard owners, lawmakers, steel producers) will have to come together and create a push that will then bring us closer to achieving our goals. We have already observed a lot of progress being made for the industry but there is much more that can be done. Personally, we would be extremely pleased if people who would like to join this cause got in touch with us so that we can support each other.