By Britt Boughey and Kent Warren (OMC Thermochemistry)
Process overview
At its core, the process is best described as a chemical looping or two-step reduction-oxidation cycle. In the reduction step, the active material, an iron- and aluminum-based metal oxide, is fluidized in a fluidized bed reactor and reduced in an inert environment, releasing some of its oxygen in a non-stoichiometric, endothermic reaction.

For the oxidation step, there are three basic options that we have explored thus far. In the first, steam can be fed over the now oxygen-deficient (or reduced) active material, which strips the oxygen from the steam to produce green hydrogen gas as a product. In the second option, CO2 can be used as the oxidant. Here, the reduced active material instead strips oxygen from the CO2 to produce CO. Lastly, in the third option, one can simultaneously deliver both CO2 and steam into the fluidized bed reactor. Here, the reduced metal oxide strips oxygen from both oxidant gases to make syngas, a combination of CO and H2. Importantly, the carbon-to-hydrogen ratio (or quality) of the syngas can be controlled by varying the mixture of the input gases. In both the second and third options, the CO2 is directly reduced into CO. No reverse water-gas shift reaction is required.

The oxidation reactions where hydrogen, CO, or syngas are produced are all mildly exothermic. Thus, the heat inputs required to keep the reaction in thermodynamically favorable conditions are mainly required in the reduction step. Heat to drive the reaction can come from just about any medium, but OMC is focused on commercializing the technology by using waste heat from other processes along with electric resistance heating as the heat source. Since the active materials are highly durable and continuously recycled in the process, the overall carbon intensity of the process will be determined by the percentage of heat obtained from renewable or waste sources.
Key differentiators
The interaction between the iron aluminate bed material and either the reducing or oxidizing environments is non-catalytic by nature. Thus, no catalyst of any type is consumed in this process and there is consequently no need for critical materials like noble metals, cobalt, yttrium, iridium, etc. The reactor is simply a refractory brick-lined (i.e., alumina-lined) steel vessel, and the bed material is also a mixture of iron oxide and aluminum oxide. This, “iron-aluminum sandwich,” leads to commercial configurations with low capital costs. Plant life is estimated to be 20 years or greater.
Scaling the reactor up is a straightforward process, as standard fluidized column reactor vessel dimensions and materials can be utilized. No new factories are required, and no new mass production techniques need to be created and implemented, saving both time and expense in scaling up. Furthermore, a single reactor system consisting of two columns where fluidized beds alternately oxidize and reduce to enable continuous production, could – at an industrially relevant scale – produce either 50,000+ kg of H2 per day or 500,000+ kg of syngas per day depending on C:H ratios desired.
Another material advantage is exceptional chemical stability. In an ongoing durability campaign, even after over a thousand cycles (500+ hours at process conditions), we have yet to observe any indication of degradation in yield or peak rate, any sublimation, or any change in structure. For conservatism, we project active material replacement every two years. As the active material can be synthesized for <$1 USD/kg, material replacement does not appreciably affect process economics.
Due to the use of low-cost, common materials and the fact that syngas can be made in a single step, commercial-scale CAPEX is predicted to be much lower than competing renewable approaches for hydrogen or syngas production.

Advancements in thermochemical hydrogen and fuels production
The concept of two-step thermochemical water splitting or fuel production from CO2 has been researched for decades, but progress towards successful commercialization has been impeded by a number of factors. Perhaps the most severe factor is low thermal efficiency. The active materials used in most efforts to date require massive temperature swings (> 500°C) between the endothermic reduction and exothermic oxidation steps, resulting in large unrecuperable solid sensible heat losses.
The University of Colorado (CU) Boulder discovered an earth-abundant active material that not only exhibits class-leading yields but also allows for the reduction and oxidation steps to be operated at the same temperature. This breakthrough opens the door for a highly efficient process that has OPEX markedly better than competing renewable approaches. OMC was formed around the exclusive license to this breakthrough in active material formulation, as well as several other advancements from CU Boulder.
Another one of those important advancements is the discovery of improved yields by operating the oxidation step at higher pressures than that of the reduction step. Pressures as high as 35 bar have been studied. Not only does operating at such pressures increase yields, but doing so also mitigates losses otherwise associated with downstream product (e.g., H2 or syngas) compression.
Two-step thermochemical hydrogen and fuel production technologies have also been almost exclusively tied to concentrating solar power, which greatly limits potential operational sites while imposing low-capacity factors and high capital costs. By shifting to electrical and waste heat to drive the reaction, OMC can globally deploy industrially integrated, low-cost systems.
Current status
Along with the aforementioned ongoing durability campaign, OMC has supported the development of an integrated prototype reactor at CU Boulder, one that is capable of producing 30kg of syngas per day in a configuration that resembles what we project a commercial-scale reactor will likely adopt. Here, efforts are underway to formally establish the record-breaking energetic efficiencies that CU’s innovations in material formulation and operating strategy (i.e., isothermal, pressure swing) consequently enable.
OMC seeks to begin design work on a pilot facility in the next few months and work on its detailed design in 2024. To this end, OMC is looking for partners that have underutilized waste heat and CO2 emissions or have an interest in low-cost hydrogen production and/or reduction of CO2 into CO or syngas.
Potential applications
OMC’s process can utilize waste heat across a broad range of temperatures, including up to blast furnace temperatures. In principle, the more waste heat available, the less heat is needed to directly support the OMC process. In this manner, the ability for heat integration could lead to a much lower balance of plant energy consumption when compared to competing approaches, such as low-temperature electrolysis.
Furthermore, OMC’s process could convert CO2 from existing steelmaking processes into CO or syngas (if H2O was also a reactant), which could be recycled back into the steelmaking process as a reducing gas, thus greatly lowering overall process CO2 emissions. By circumventing the need for a catalyst, OMC’s technology is intrinsically tolerant to impurities in flue gas streams. We look forward to discussing gas compositions and their process implications with interested parties.
If usage as a reducing process gas is not desired, there are multiple mature conversion technologies for upgrading syngas into products such as diesel and jet fuel, lubricants, chemical precursors such as ethylene, or alcohols such as methanol or ethanol. These may present higher economic value than use as a reducing gas while still lowering the carbon intensity of the produced steel.
OMC could also supply hydrogen to any current need or in the future Direct Reduction of Iron facilities. The potential for heat integration and the ability to rapidly scale to commercial volumes could change what is possible in this field in both aspects of cost and deployment times.
The authors
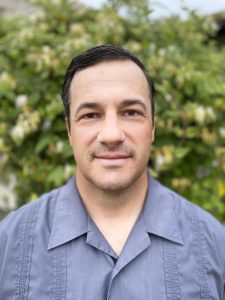
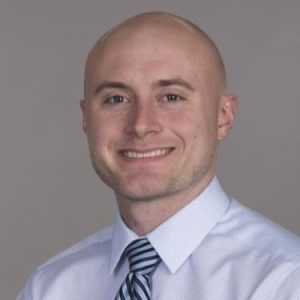