From all perspectives, we cannot afford to take a step backwards. We must find success in change and continue to advance our lives and enjoyment. An immense challenge, sure, but also an exciting one -provided we put our hearts, our science and our full commitment into it.
Among strong competition in the stainless steel industry, Aperam is one of the first companies to have undergone a profound transformation in order to achieve the ambitious goal of reaching carbon net zero by 2050. The company profoundly changed its strategy last year to decarbonize its operations in the broadest possible sense (scope 3, see diagram). This sparked an ongoing revolutionary improvement process.
“Internally, we have created an organisation that is well-positioned to achieve this goal,” says Aperam Chief Technology and Sustainability Officer Bernard Hallemans. “We are reshaping our structure to the core and we have clearly adopted a roadmap to become a leader in this virtuous race.”
As Hallemans points out, stainless steel is a sustainable material. “We know that it is a real solution for the future, and an industrial priority that brings environmental benefits in many sectors,” he explains. “The question is how to transform Aperam into a company that not only supplies quality steel, but does so in a way that is neutral or even positive in terms of environmental impact?”
As Aperam tackles the subject of CO2, Hallemans notes that things are moving even faster than expected. For example, following the classification of the greenhouse gas protocol, the company has already engaged in substantial reductions on scope 1 and 2 (direct and part of indirect production emissions, see diagram) per our 2030 goals, putting Aperam well on its way to reaching carbon net zero by 2050. Not being one to rest on its laurels, Aperam is already focused on the more challenging scope 3 emissions, which is much broader and involves a major effort on raw materials used in this industry. The company is actively collaborating with its suppliers and customers, all of whom must adopt the principles of the circular economy.
Aperam itself is also making changes. For instance, it is urgently working to ‘close the loop’ by collecting as much scrap as possible to feed back into the production chain. The ultimate goal is to base our products on 100% scrap. “We are moving towards completely reinvented supply chains, enabling us to collect the raw material more efficiently, sort it, and process it to obtain perfectly recycled steel,” adds Hallemans.
“Our specific strength is that, as an integrated company, we have good control over our supply chain,” continues Hallemans. “As the steel is recycled, it retains all its properties, and Aperam’s manufacturing benefits from the most cutting-edge quality control techniques, guaranteeing impeccable products for consumers while also endorsing the principals of recycling, reuse and
renewables.”
But, as Hallemans is quick to point out, while processes and raw materials are important, one cannot ignore the human factor. For Aperam, the challenge is ensuring that its approximately 11,000 employees are fully engaged with the transformation. “At Aperam, we aim to ensure that all our employees feel like ambassadors for the company’s efforts,” says Hallemans. “After all, the expertise and desire for change ultimately stems from them: in addition to being employees, they are also consumers.” As consumers who are also familiar with the sustainable benefits of stainless steel, Aperam’s employees are particularly well-positioned to advocate for making the switch from plastic to stainless products. “A large proportion of our staff are actively involved in transforming the company, but all of them have this purpose in mind,” remarks Hallemans. “Implementing the closed loop is a huge challenge, but I’ve noticed that it generates a great deal of enthusiasm among our people.”
Forests in Brazil: carbon sink and clean energy
Aperam’s sustainability revolution goes well beyond the shopfloor, it extends to every facet of the company – including in South America. To learn more, we talk with Frederico Ayres Lima, CEO and CMO Stainless & Electrical Steel South America.
According to Lima, if complete sustainability is to be achieved, it will be thanks to a sustained effort on the part of the company’s many collaborators. In Brazil, these collaborators include a foundation
that supports economical, cultural and educational private investment projects happening in the communities where Aperam is an active player.
“When I joined the company 26 years ago, corporate social awareness was extremely rare,” recalls Lima. “We were already being asked questions about our personal organisation, how to adapt to our needs, and I always learned a lot on this topic – something that I continue to take constant care of today.” The benefits of this commitment were seen at the latest in-house health and safety event, where well-deserved awards were handed out. “The company has once again beaten its own records in terms of safety,” notes Lima. “For Aperam, safety is an imperative that outweighs all others, including financial ones.”
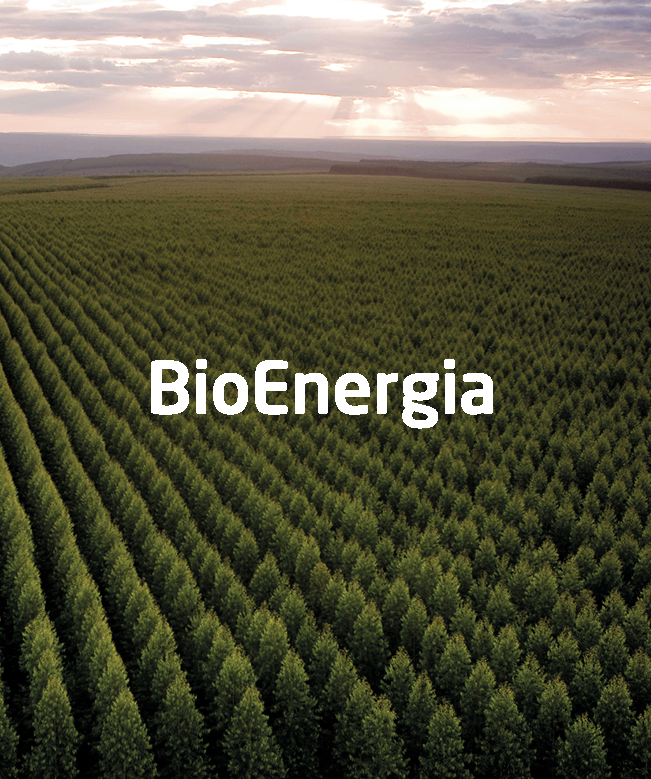
It must be pointed out that the challenges are numerous, given the wide range of activities carried out by the Group in South America. In addition to producing steel, the company also oversees BioEnergia, the management and development of an immense forest from which bio-sourced charcoal is produced and used to provide the energy needed for the blast furnaces used in the industrial plant in Timóteo MG. “The CO2 produced when using these furnaces is entirely, and directly, cancelled out by the capture of the trees managed by Aperam,” adds Lima. “In fact, 95% of the energy we use is renewable, and the use of coke is now a distant memory.”
While becoming one of the world´s largest charcoal producers is quite the accomplishment itself, Aperam has also learned another new trade: forestry management. Its expertise is now well-established, as the company is ahead of the regulations and complies with all FSC® management standards.
As Lima explains, managing a forest involves more than just trees. Instead, forests are like mosaics, to prevent the spread of disease, different species are grown simultaneously. It also includes the many animals that call the forest home. “One of Aperam’s challenges is to continually increase biodiversity on its land,” comments Lima. “We want to make the most of Brazil, which, thanks to its climate and vastness, offers us the opportunity to develop such large areas of timber land.”
BioEnergia is one of several levers that Aperam South America uses to reach one of the lowest CO2 emissions among blast furnace steel producers (scope 1 + 2 + 3a). Looking back at the progress made over the course of the past year, Lima highlights several important achievements. “We are both widely recognised as a good company to work for and have been able to invest in expanding the forest,” he says. “Furthermore, we have shifted our business model so we are not only a steel producer, but are now also selling seeds, patents and forest management services, which accounts for a real part of our business – who would have thought!”

Closing the loop
That being said, Aperam’s core business remains making the highest quality stainless steel.
One of the major fronts in its battle for carbon neutrality is the sourcing of metals. Although the company is highly integrated, it does not manage any mines anywhere in the world. Instead, it focuses on recycling, which poses a major new challenge: how to maximise the collection of used products containing steel, organise a precise sorting of the metallurgical components, and re-inject this into Aperam’s production?
The necessary resources for answering this challenge are already in place. This starts with Recyco, Aperam’s recycling unit dedicated to recovering and treating the metallic content from melting shop dust and sludge. Aperam treats the residues of former smelting furnaces and recovers the metals for reuse. It also specialises in managing and promoting the reuse of remaining by-products, a technological jewel in the Group’s ecosystem.
With the German-based ELG unit, which Aperam acquired at the end of 2021, the company now boasts a new expertise: that of the efficient recovery of metals produced throughout the world.
ELG is one of the world leaders in this domain and, as a result, Aperam’s ambition of ‘closing the loop’ in stainless steel production by relying on existing raw material gets closer by the day. This is already the case for certain metals, such as titanium, which is also processed by ELG.

steel industry, as well as high performance
materials such as superalloys and titanium.
In fact, it has just been revealed that the subsidiary has formed a partnership with IperionX to set up a totally closed-circuit supply chain. The recycled output will be used in such highly complex industries as aerospace, electric vehicles and 3D printing.
Aperam’s own processes are reshaping entire industrial sectors. More than a pledge, all of these represent concrete steps towards reducing Scope 3 CO2 emissions. Of course, this level of business integration requires ongoing adaptation and synergies, which is what Aperam has been enthusiastically doing during the past year.
With Recyco and ELG, two benchmark companies, the Group has boldly redesigned its strategy and is now beginning to reap the rewards.
Metal made of… plants
Aperam’s recycling strategy also includes a complementary – and impressive – pillar.
Steel production requires a constant rebalancing of alloys with fine supplements to obtain the right quality. Alongside ELG and Recyco, Aperam has chosen to embark on a unique ‘soft’ sourcing: agromining.
In partnership with the biotechnology company Econick, Aperam founded Botanickel, a research and industrial company that will make it possible to extract nickel from plants. “We want to be the pioneer and benchmark for this method of extraction, right down to stainless steel, with the strictest respect for co-development with local communities, climate, and biodiversity,” says Botanickel chairman Aurélien Buteri.
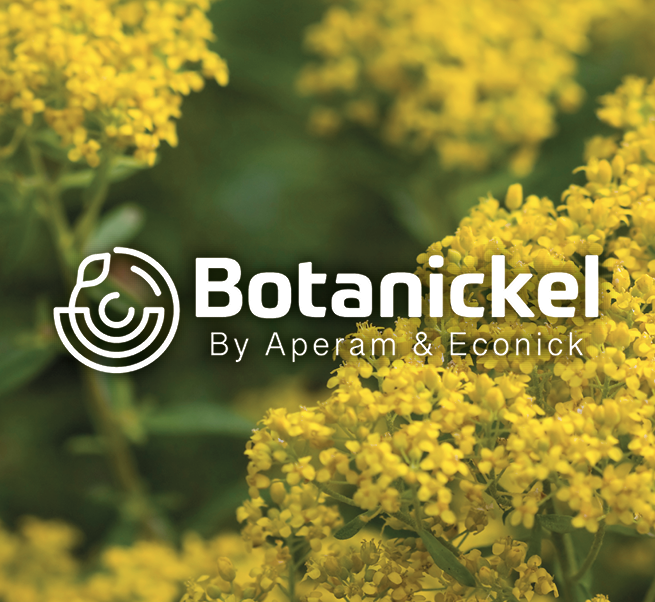
Botanickel, which has harvested its first batches of biomass, exploits local endemic plants on nickel-rich land, always optimising what already exists and thus opening up new opportunities for agricultural areas. This innovation has been fully integrated into the new value chain that Aperam is now defining. Furthermore, Botanickel has already established itself as an acclaimed and sought-after scientific reference, consulted for agronomy and industrial feasibility projects, and for land diagnostics.
2023 has seen the launch of Botanickel’s industrial phase, with the recruitment of men and women who will lead the project, providing the Aperam Group with a real biosourced metal supply.
Isn’t that what writing your own future is all about? Aperam is doing so with a great deal of success and, most of all, with an unalterable will.