Photo: Johnson Matthey © 2025
For over 200 years, Johnson Matthey (JM) has been at the forefront of addressing some of the world’s most pressing challenges. Beginning with their expertise in platinum group metal (PGM) chemistry, JM’s journey has spanned diverse areas of material science and clean technology. Their work in refining and recycling PGMs has positioned them as leaders in the field, especially in catalysis, where these metals excel.
One of their landmark achievements is the development of the three-way catalytic converter for internal combustion engines, a technology now celebrating 50 years. This innovation, which utilizes PGMs, has been instrumental in reducing harmful emissions from engine exhausts.
JM’s success in catalysis laid the groundwork for their expansion into process technology. Over time, the company diversified into non-PGM catalysts and strengthened its portfolio through strategic acquisitions. “This has provided us with several number-one technologies that play a critical role in the built environment,” noted Dr. Eugene McKenna. “For example, we have made significant advancements in methanol and low carbon hydrogen-related technologies.”
As the energy transition accelerates, JM has pivoted to use its expertise for a more sustainable future. Hydrogen has become a central focus, driven by the key role PGMs play in PEM (proton exchange membrane) electrolysis and by the syngas technologies that can decarbonize the industry in scale.
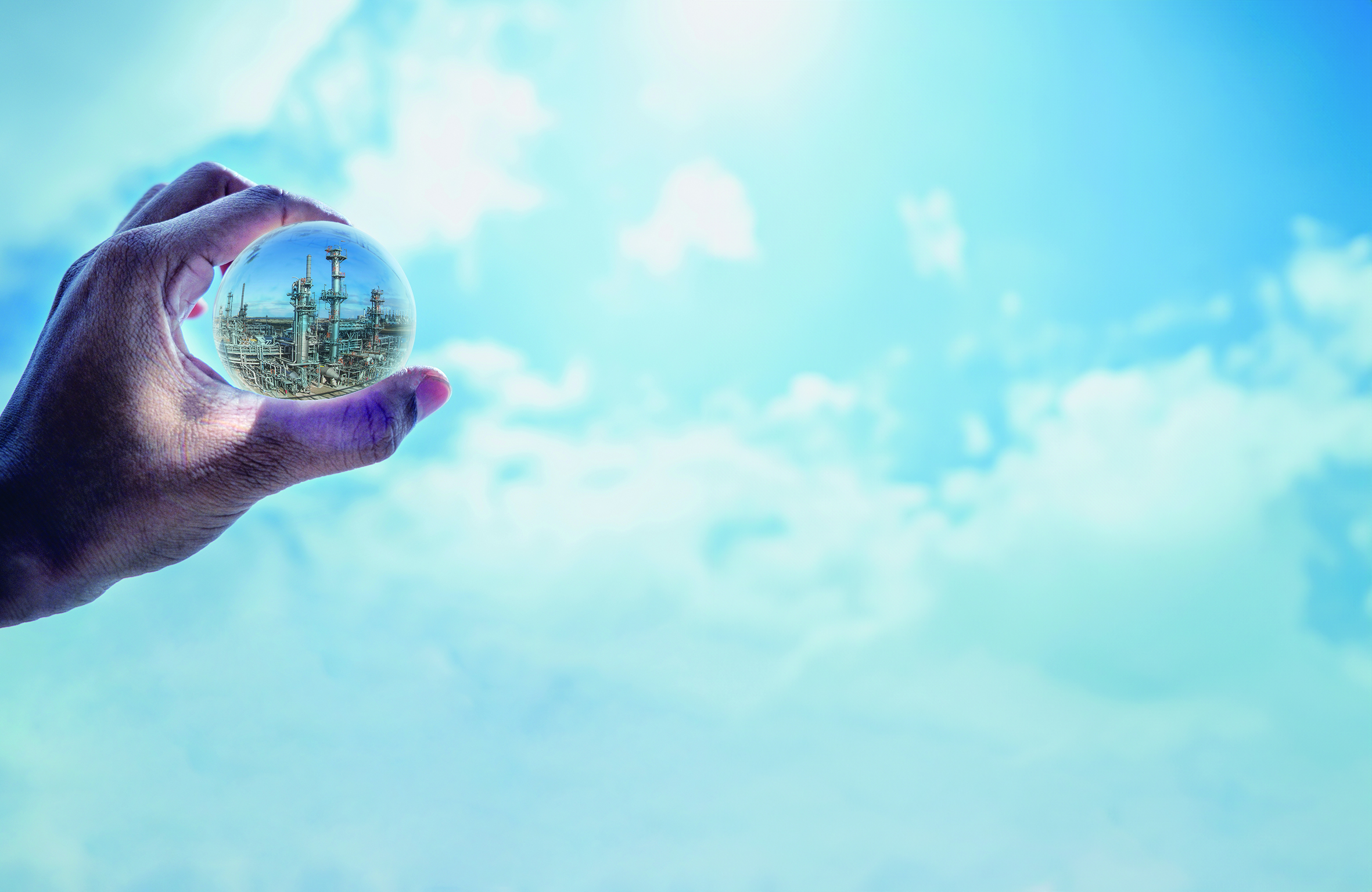
PEM Electrolysis
“We manufacture critical components for PEM electrolyzers that produce green hydrogen, enhancing the efficiency of the process. These same components are also used in fuel cells,” explained Dr. McKenna. “When hydrogen is used in a fuel cell, it generates electricity electrochemically, with water as the only byproduct. This allows fuel cells to produce power without harmful emissions or particulates, offering a potential replacement for internal combustion engines.”
From purifying the PGMs essential for hydrogen production direct from mining to recycling these materials, JM is deeply embedded in the hydrogen value chain. “This naturally brings us to industries like steel, where hydrogen is critical for decarbonization,” Dr. McKenna emphasized. “Iron and steel manufacturing currently accounts for about 8% of global greenhouse gas emissions. Decarbonizing this sector is vital, and hydrogen is central to that effort.”
Low carbon hydrogen technology
JM has long been involved in autothermal reforming (ATR), a syngas technology central to producing low-carbon hydrogen—commonly known as blue hydrogen—via natural gas with carbon capture and storage (CCS). Dr. McKenna highlighted the company’s extensive experience:
“For decades, we have specialized in syngas technologies, which have been critical for producing chemical building blocks like methanol, formaldehyde, and ammonia. Long before the focus was on clean hydrogen production, JM was already optimizing these processes to enhance efficiency. Today, we are the leading technology provider in the methanol sector, an industry of significant global importance.”
JM’s expertise in methanol production proved to be a strong foundation for advancing blue hydrogen technology. “Our process for making hydrogen from natural gas is uniquely efficient,” Dr. McKenna explained. “In traditional steam methane reforming (SMR) systems, heat is supplied by burning gas externally to the reaction vessel, resulting in flue gases with low concentrations of carbon dioxide (CO₂) mixed with nitrogen. Capturing CO₂ from this setup is energy-intensive and capital-heavy.”

In contrast, JM’s ATR process integrates heat generation within the reaction vessel itself, offering several significant advantages. First, the carbon dioxide (CO₂) produced is entirely contained within the process stream at high pressure and purity, which greatly simplifies its capture. Second, by eliminating the need for external combustion and the associated flue gases, the capital expenditure (CapEx) required for CO₂ capture is reduced compared to traditional methods. Lastly, JM’s technology maximizes efficiency by minimizing natural gas usage per kilogram of hydrogen produced, generating less CO₂, and enabling the capture of up to 99% of the CO₂ generated during the process.
“This approach offers the lowest cost pathway for converting natural gas to hydrogen, provided the process is optimized,” Dr. McKenna emphasized. “While costs depend on factors such as natural gas prices, our technique consistently delivers the highest value-add from gas to hydrogen.”
JM’s commitment to advancing clean hydrogen production is evident in its focus on efficiency and scalability. “We have prioritized a process that excels at producing hydrogen at the lowest possible cost with minimal environmental impact,” he concluded.
Can the industry go green?
Dr. McKenna reflects on the challenges of transitioning to a green economy, noting a shift in focus over recent years. “Three or four years ago, we were discussing plans and setting targets. Now, as the first milestones approach, it is becoming clear just how challenging this transition is and how serious we need to be about the steps we take to make it happen,” he observed. Despite the hurdles, he is optimistic that the mechanisms and technologies being implemented are making a tangible difference.
“For instance, the first projects producing blue hydrogen have now reached final investment decisions (FID), and there is a significant pipeline of similar projects underway,” he shared. “When it comes to the broader energy transition, it is evident that there is no path to net-zero without clean hydrogen, and we are already seeing momentum in this area.”
Dr. McKenna also highlighted legislative developments driving change. “In the European Union, measures like the ETS (Emissions Trading System), the carbon tax, and the carbon border adjustment mechanism are incentivizing the production of clean steel while discouraging conventional steelmaking. These policies strongly favour clean steel, but they also raise critical debates about balancing the costs of going green with the risk of deindustrialization,” he explained. “This is the global challenge we face—can the industry go green before it grinds to a halt?”
Dr. McKenna acknowledged that while the necessary technologies and policy instruments are understood, the sector is only beginning to experience the growing pains associated with this transformation. “The technology is proven, and the policies to support its adoption are known. Yet, we are in the early stages of the difficult adjustments required, and the industry is under significant stress,” he concluded.
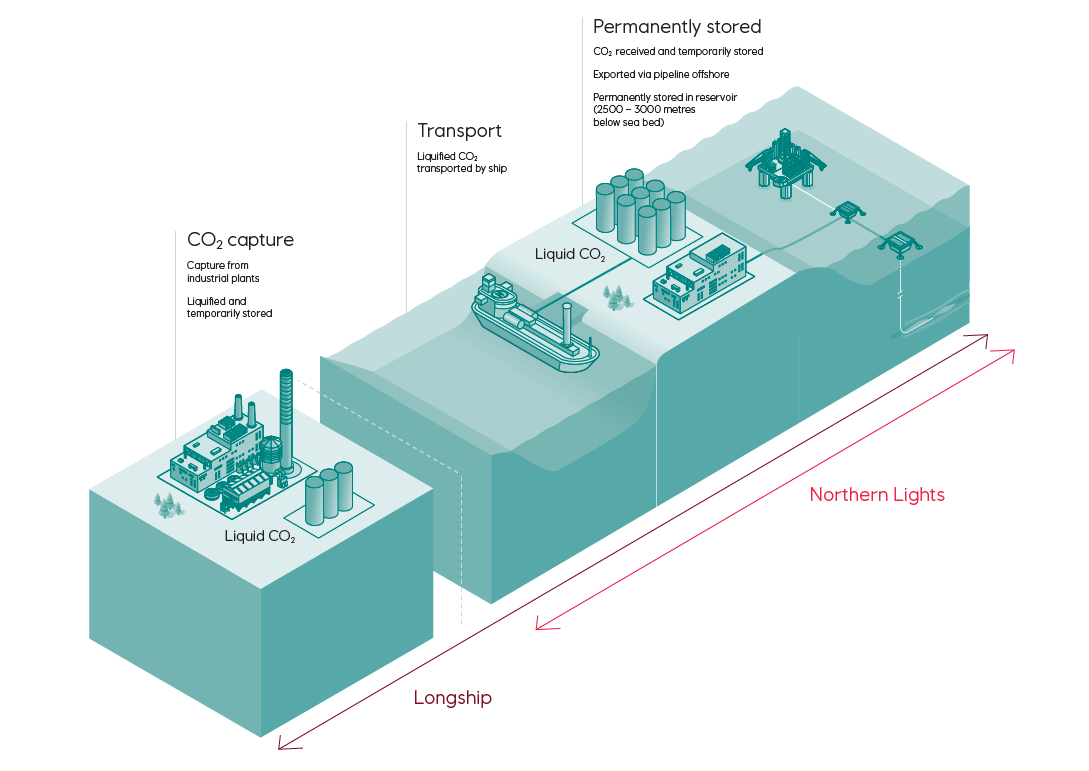
Hurdles and solutions
In the energy transition, it is crucial to step back and view the broader system to understand its complexities. Dr. McKenna points out that the best access to renewable energy—and therefore green hydrogen—will be in regions rich in sunlight and wind, such as the Middle East, Australia, Brazil, Namibia, and parts of Africa.
The main challenge lies in transporting this energy from resource-rich areas to high-demand regions like Europe and Asia. While hydrogen offers a promising solution for moving energy across time and space, its logistics remain complicated. Today, hydrogen production is already significant, particularly for industries like steel, but global transportation requires new infrastructure, similar to what was developed for LNG decades ago.
The current debate centers on the most efficient way to transport hydrogen. Liquefied hydrogen is one option, but it requires extremely low temperatures and high pressures, making it costly. Another approach involves converting hydrogen into ammonia, a carbon-free molecule that is easier to ship and already moved globally at scale. However, converting hydrogen into ammonia and back reduces energy efficiency. Methanol is another potential carrier, but it introduces complications due to its CO₂ content, requiring careful management of emissions. Pipelines may be viable for shorter distances, such as transporting hydrogen from North Africa to Europe, but they are not practical on a global scale.
An alternative worth considering, particularly for the steel industry, is producing low-grade iron in hydrogen-rich locations and shipping it to Europe or Asia for processing into steel using electric arc furnaces. This could reduce the need to transport hydrogen itself while creating opportunities for industrial realignment.
The global energy transition is not only a technological challenge but also an economic and political one. As Dr. McKenna notes, “The solution will reflect a mix of engineering, economic pressures, and political decisions. It will not necessarily only align with the ideal technological approach.”
The role of hydrogen in the energy transition
“The scientific consensus is clear: the energy transition cannot succeed without hydrogen. While some processes can be electrified or powered by alternative solutions, others—especially large-scale industries like steel and iron production—are entirely reliant on hydrogen for decarbonization,” explained Dr. McKenna.
Dr. McKenna argues that scepticism surrounding hydrogen often arises from a misunderstanding. Critics may question its viability while maintaining faith in the broader energy transition. However, these views are incompatible. Hydrogen is essential for achieving net-zero emissions, and its role must scale dramatically. The question is not whether hydrogen will be crucial but how quickly it will be implemented—and how much of the carbon budget will be consumed before it becomes widespread. Effective coordination and regulation can accelerate this process, minimizing global temperature increases.

Hydrogen will find its place where it provides the most cost-effective pathway to clean production. Market forces should naturally determine its applications: hydrogen will be chosen for processes it uniquely suits, while electricity will dominate where it is more efficient.
Early adoption is likely in industries or markets willing to pay a premium for sustainability. For instance, green steel could initially be positioned as a luxury product, appealing to buyers invested in environmental responsibility. Dr. McKenna likens this to the initial adoption of safety technologies like airbags, which began as premium features but became mainstream through economies of scale.
As green steel establishes itself, economies of scale will drive costs down and broaden accessibility. Similarly, hydrogen’s scaling will reduce reliance on government intervention. When the system works as intended, hydrogen’s role in the energy transition will feel natural, dictated by necessity and market dynamics.
“From a business perspective, hydrogen represents a significant market opportunity for both our products and our customers,” said Dr. McKenna. “More importantly, it aligns with our mission to catalyze the energy transition. Decarbonizing industries and reducing carbon intensity are at the heart of this mission, and we see ourselves playing a critical role by enabling low-carbon hydrogen production—whether through electrolytic or thermochemical methods.”
While substantial progress has been made in stimulating hydrogen production and developing its supply chain, sufficient demand remains a challenge. A key opportunity lies in Europe’s steel industry, which could drive hydrogen demand at scale. However, this requires the right regulatory framework to make investments in hydrogen-powered steel production viable.
“Creating such demand would not only advance the steel industry’s decarbonization but also strengthen the entire hydrogen value chain, ensuring its scalability and long-term success,” Dr. McKenna concluded.